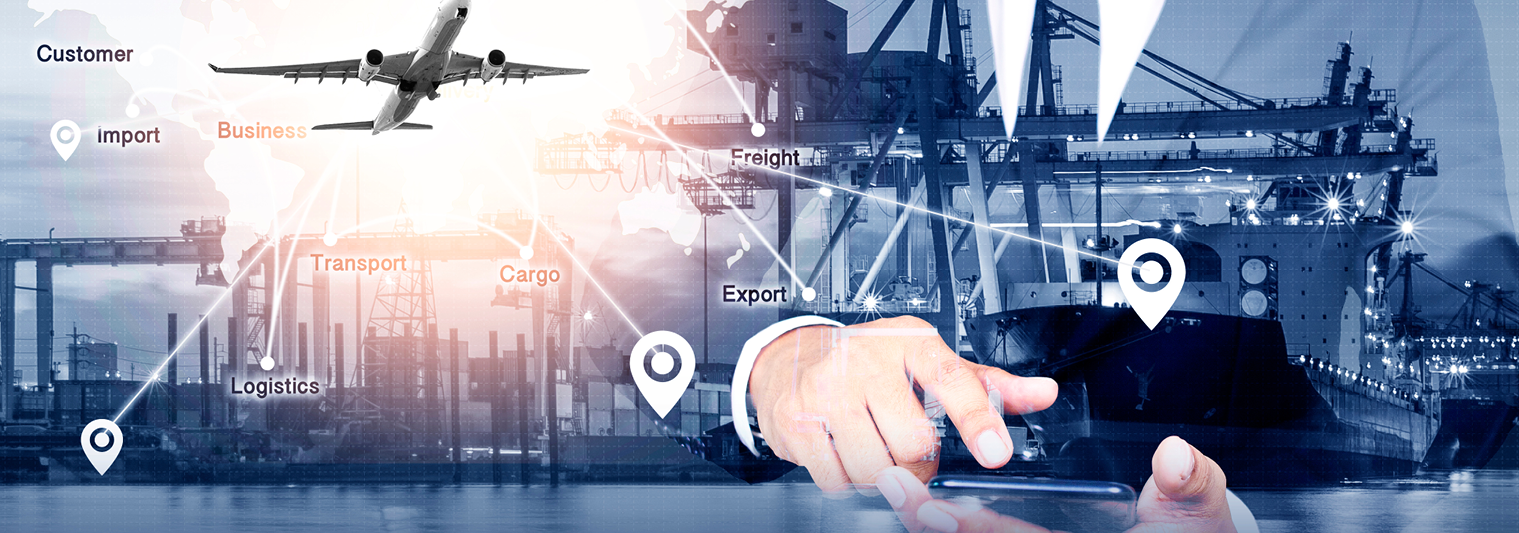
Let’s explore the reasons for the current explosion in decentralized inventory, the warehouse implications and what companies can do to manage the increased complexity.
First some Supply Chain theory. The debate between centralized and decentralized inventory is as old as Supply Chain Management itself. It focuses on the pros/cons of holding inventory in one large central warehouse (centralized inventory) versus multiple smaller warehouses (decentralized inventory). Typically, cost modelling will show a central warehouse reduces overall inventory levels, working capital costs and warehouse costs versus decentralized warehouses. However, a centralized model leads to higher transport costs because of the greater distance to the customer base. The “right” number of warehouses to serve the market becomes a trade-off between warehouse costs and transport costs, but critically customer service needs to be considered. If it takes 3 days to process and deliver an order from the central warehouse to the customer but the customer needs delivery in 2 days, then one central warehouse will be insufficient.
The importance of customer service when designing an optimum warehouse network is clear. The big trend in recent years has been towards reduced lead times, the so called, Amazon Effect, with rapidly evolving customer delivery expectations, from a few days, to next day, to same day and now to 2-hour delivery! The Amazon Effect is forcing retail and other e-commerce companies to hold inventory in smaller warehouses closer to the customer, as the only way to guarantee meeting these service standards. This trend to decentralised inventory is also seen in other industry sectors:
- The Direct to Consumer (DtC) model is a growing trend in the Consumer Packaged Goods (CPG) sector. With DtC the CPG company delivers direct to the consumer bypassing the usual wholesaler or retailer. The benefits for the CPG are improved margins and a closer relationship with their consumer. Many CPG companies started pilots of DtC based on a small range of products but it has quickly evolved into a growth engine accounting for over 20% of sales. Companies using the DtC model include Nike, Unilever, P&G and Heineken. DtC has a big impact on the Supply Chain because now the CPG has to hold inventory in smaller warehouses closer to the consumer and manage home deliveries with all the usual “final-mile” challenges.
- The provision of Aftermarket service for spare parts is a critical requirement in many industries including oil and gas, mining, automotive, rail, aviation, telecommunications and industrial manufacturing. These are asset intensive industries where plant downtime resulting from equipment breakdown can have huge cost implications. Service is paramount and customers are demanding smaller and faster deliveries. This requires changes in network design with more inventory locations closer to the customer. BT is the major fixed line telecommunications provider in the UK and they also provide third party logistics services to other utility companies through a subsidiary, BT Supply Chain. One of their customers is EDF Energy who are in the process of rolling a smart meter programme to over six million residential and small business customers. BT serve EDF from a central warehouse and a national network of locker pick-up points where the smart meters are picked up by EDF field engineers. Replaced meters get returned through the same network. BT operates 1,800 lockers across the UK with 24/7 access and claim no field engineer will ever be more than 15 minutes’ drive from a locker.
Taken together these industry trends are leading to an increase in demand for smaller warehouses close to urban areas. In the US, buoyant demand for warehouse space in 2019 has driven vacancy rates to an all-time low of 4.8 per cent, with the overall vacancy level cut in half since the beginning of 2010. European warehousing started the year with historically low vacancy rates of well below 5 per cent. According to CBRE, the property company, US demand for warehouse space has outstripped supply since 2010. The problem is acutest in urban areas, such as, Los Angles, San Francisco and New York. Increased demand for urban warehouse space and consequent shortages have led to companies getting creative:
- The decline in traditional bricks and mortar retailers has freed up retail stores which can be used for warehousing. Downtown office space is also been used for storage by companies like Amazon to meet those 2 hour lead times.
- Buildings are not a prerequisite - lockers and vans can be used for storage as well.
- Pop-up or On-Demand warehousing is like the Airbnb of warehousing where online marketplaces are used to match supply and demand for space. Rentals can be for short periods meaning that companies are not locked into long, inflexible multi-year lease agreements. Flexe in the US. and Stowga in the UK operate such marketplaces. The On-Demand model is also useful for companies who need to manage seasonal peaks in business, including Christmas and Black Friday.
A critical consequences of decentralized inventory is increased Supply Chain complexity. A myriad of new inventory holding locations, from vans to lockers, need to be managed to ensure customer service requirement are achieved. A recommended approach:
Use the Enterprise Resource Planning (ERP) system:
Companies have sometimes taken a short term view of these smaller inventory locations and attempted to manage them outside the system. In our experience this can lead to poor inventory controls and moreover a big impact on customer service. It’s worth investing the time to set up the inventory locations in your Enterprise Resource Planning (ERP) System and to automate the key business processes.
Inventory Replenishment:
The ERP system can then be used to manage inventory replenishment to these new stock holding locations. They are physically, smaller than traditional warehouses and hold less inventory buffer, which puts the onus on a robust replenishment process based on high inventory accuracy.
Inventory Accuracy:
A third area that needs focus is the whole inventory control process in each location. Its really important to capture accurate receipts of products and issues to maintain inventory accuracy and high levels of customer service. Again, we wouldn’t recommend a manual paper based process, which is time-consuming and error prone. Goods receipts and issues can be automated using bar coding and handheld scanners linked directly to your backend ERP system. In this way you capture movements in real time and your ERP inventory will always align with physical inventory. A solution such as Innovapptive’s mInventory provides goods receipt, goods issue, stock overview and inventory counting. This system can run on any smart phone so you don’t need to deploy expensive industrial scanners.
- The last area that companies need to consider is the challenge of the “final mile”. Traffic congestion, customer not-in, redeliveries and returns all need to be managed. It’s a lot harder to deliver to a customer’s home than a retailer’s Regional Distribution Centre! Good reasons why most companies have chosen to outsource the “final mile”
Many industry sectors are faced with the challenge of inventory decentralization driven by new business models and increasing customer requirements. If your business is faced by the challenge of decentralized inventory or you’re interested to learn more, then please reach out to Innovapptive for a more detailed discussion.