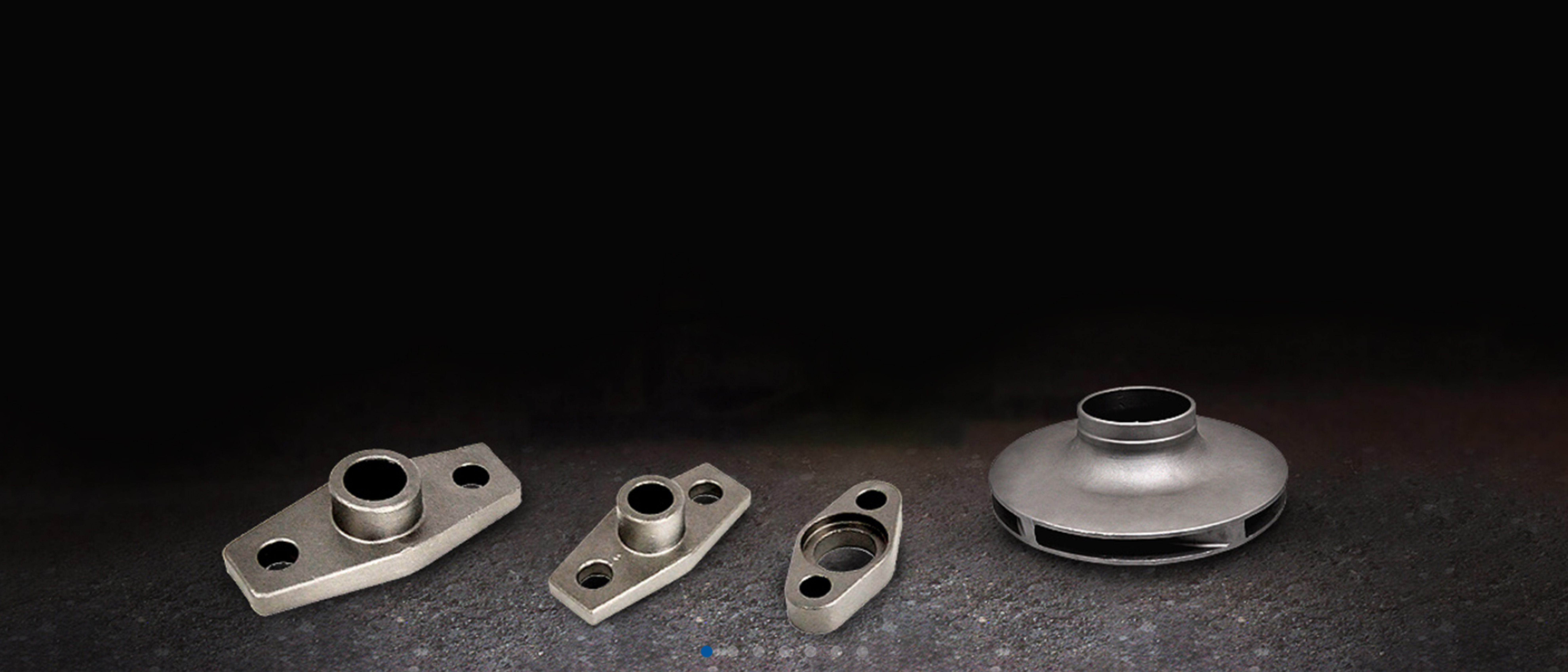
Micro fusion Investment Casting Process
To understand the process completely here’s a brief account of the micro fusion investment casting process and how it’s done to produce high-quality casting products.
- Die/Tool Preparation- A tool or die is made with the help of machines and the cavities in the tool are made in the same pattern as the original cast and after that pressurized wax is filled in this cavity to obtain a distinctive and specific wax pattern.
- Wax Pattern Making- Petroleum wax or any other specialized wax can be used for pattern creation. For this, the wax is melted and prepared following the QCP requirement of the wax pattern and is kept in the semi-liquid form.
This is attained by first feeding the wax pattern into the hydraulic injection press and this is followed by injecting the wax into the hollow tool. Then the injected wax is allowed to get cooled and solidified to take the form of the metal cast.
- Shell making with ceramic coating- After completion of the wax pattern formation, the gating assembly is made by the process of making runner, riser, and spur.
The repetitive dipping process in the ceramic slurry is known as the secondary process and it helps in strengthening the shell mold.
- Dewaxing process, melting and pouring of the metal- To make room for the pouring of the melted metal the ceramic shell undergoes the process of dewaxing.
To remove any traces of remaining wax from the shell it is then baked in a furnace. This not only burns any remaining wax left in the assembly but also makes the shell compatible to withstand the high temperature of liquid metal that will be poured into it. After the shell has gained the strength to contain the melted metal without reacting to it, then the melted metal is poured into it.
- Shell Discard- After the poured metal is cooled and solidified, there is no need for the outer ceramic shell and hence it is removed by breaking it into the pieces.
The metal cast is removed and undergoes the heat treatment process to acquire the mechanical properties of the casting.
- Fettling and machining- Grit blasting and pneumatic grinding are used to give final finishing to the desired metal cast. The finished casting is duly machined and semi assembly and machined casting are done to obtain the final product.
- Final inspection- Visual tests are conducted to get 100% of finished products. The metal casts are duly checked on all the parameters to assure the quality and standard of the final finished product.
Microfusion Casting Process in India
The micro fusion investment casting processes and system should be approved by the world’s leading and notifying agencies to assure product quality.
The products manufactured by the process of micro fusion must follow the international standards and should be made as per the requirements of the domestic and international OEMs.
The final metal products need to be treated with the same expertise and experience. Purchasing high-quality approved products can be safely used as parts of any machinery. Thus, the process of micro fusion needs to assure product quality.