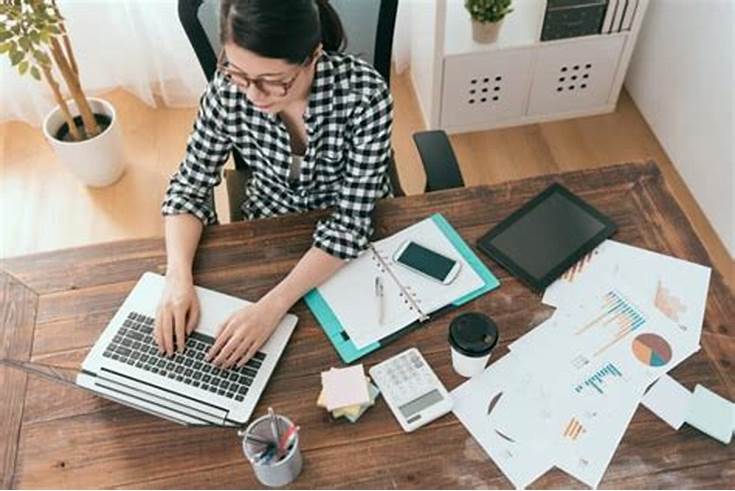
A barcode inventory system is one in which each product is assigned a unique barcode. When a product is sold, the Barcode Inventory System for Small Business is scanned, and data is sent to a central database.
As a result, when an item is chosen. When picking a product, the warehouse worker scans the barcode. The scanner then informs the worker if they have selected the correct item. It also logs the action in your inventory management system, allowing you to keep track of stock levels more accurately. Assisting you in keeping a real-time inventory track and improving picking speed and accuracy.
What kind of information can a barcode hold?
Barcodes can hold a lot of information that your inventory management system can use. A barcode, for example, can convey information such as a product's name, weight, dimensions, and warehouse location. However, for efficient picking, you would generally not use the barcode to store such specific information, but rather a unique string of digits to ensure the correct item is picked.
What are the various types of barcodes?
You are probably most familiar with these types of barcodes. They consist of vertical black lines. The space between the lines is then used by the scanner to determine which product it is looking at.
These are typically square in shape and have various shaped shapes that are used to store data. They are used when more information than a 1D barcode can be stored.
Setting up a Barcode Inventory System
Putting together a barcode inventory system is surprisingly simple.
Step 1: Make a product code.
The first step is to generate a product code. These can be based on a 12-digit UPC (Universal Product Code) or SKU (Stock Keeping Unit) number. While the former has advantages, most ecommerce businesses begin with SKU numbers. However, if you are not manufacturing the products yourself, it is likely that the products you purchase will already be barcoded.
Step 2: Make a barcode
The following step is to generate a barcode for each of your product's codes. To accomplish this, you can use barcode software or an online barcode generator.
Step 3: Create a barcode.
To print your barcode, you'll need an inkjet or laser printer, though thermal printers are preferable.
Step 4 – Insert the barcode into the appropriate location.
The barcode is then printed and placed in the appropriate bin, shelf, or product. Pickers then scan the barcode as they select an item. Wherever possible, I would recommend placing the barcode on the product itself. This eliminates the possibility of human error, such as putting a product in the wrong bin or shelf.
What is the operation of a barcode inventory system?
Barcodes connect the data gathered during picking to your inventory tracking system. So, when the barcode is scanned, it notifies the picker that they have selected the correct item and notifies your inventory management system that the correct item has been selected. In your live inventory tracking, reflect the new figure.
So, on the one hand, it makes your pickers' lives easier while also reducing mispicks. On the other hand, it provides an accurate real-time live inventory count.
The Benefits of a Barcode Inventory System
Fewer blunders
People become fatigued and distracted. Especially when they are pressed for time. This also applies to your selection team. If you rely on your pickers to choose the correct item every time, they will make mistakes. Mistakes result in mispicks and customers receiving the incorrect item.
As the video below from our recent Black Friday webinar shows, barcoding your products can have a significant impact on high-volume days like Black Friday.
For example, a common scenario that businesses face is:
- A picker makes a mistake (which wastes time)
- A customer receives the incorrect item (which frustrates them)
- A customer service representative must then deal with the customer and correct the error (so more lost time and either a refund or replacement)
- The picker must then select the correct item (So more time is being spent on the same order)
- After that, the item is shipped (costing more money)
When a Warehouse Management System for Small Business is scanned, the scanner ‘checks' that the correct item is selected. As a result, no matter how tired they are or how busy things get, it will be easier for them to choose the right item. As a result, the scenario described above is unnecessary.
TCO, for example, reduced their mispick rate by 91 percent after switching to a barcode inventory system.