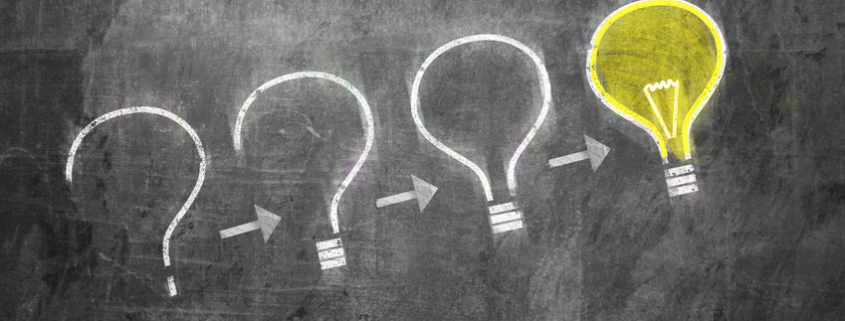
Problems arise in the business world. And it's comforting to know that many of them are avoidable with the right tools. This is where process behaviour charts come into play. They are used in a wide range of industries, particularly manufacturing, to determine whether a process is stable and under control.
Using a data-driven approach, these charts visually monitor the performance of a process. When used correctly, they can provide you with the ability to prevent problems from occurring in real time. In the case of manufacturing, this means that a company can avoid issues such as costly downtime. As a result, process behaviour charts are an invaluable tool in this regard.
Aside from that, process behaviour charts can do a lot more. Here are some of the additional advantages of implementing them in your organisation.
They alert you when there is a problem with a process.
It can be difficult to tell when a process is in trouble and needs to be modified. You can tell when it's time to make improvements by looking at a control chart. As a result, these charts act as an early warning system, alerting you when a process is about to go awry.
As we all know, producing a subpar product can be costly in a variety of ways in the manufacturing industry. For example, if your product is of poor quality, you risk disappointing customers, who may abandon ship and seek out the competition. Using a process behaviour chart, the problem can be identified in its early stages and corrected before it becomes a serious problem.
They keep the process from being tampered with unnecessarily.
Most of the time, a process behaves as it should, so no changes are required. Tinkering with it would be considered unnecessary tampering, which could cause it to malfunction. Tampering with it may unintentionally expose it to factors that increase special cause variation, which is not the type of variation you want.
A control chart allows you to make informed decisions about the process, such as when to avoid messing with what works. When a process is working properly, the variation along the centre line will be random. This is a good time to instruct operators to do nothing and let the system do its thing until the chart indicates otherwise.
They assist you in determining whether your efforts to improve are effective.
Assume you have a process that is unstable and uncontrollable. You can make changes to it, but how will you know if your efforts were fruitful? Of course, by looking at a control chart. The chart can also notify you if your changes are having the opposite effect, i.e., making the process worse rather than better.
Process behaviour charts can give you the ability to predict the future output of a process in addition to assessing the impact of your amendments. When a process is stable and under control, it can be predictable. This type of information can help you make educated decisions.
When it comes to process improvement, they take out the guesswork.
Some people are born with the ability to repair processes. This enables them to pinpoint precisely what is wrong and how to correct it. These people operate instinctively, and looking at a process behaviour chart would simply confirm what their gut instinct has already told them.
However, not everyone has this innate ability, and they can use a control chart to level the playing field. If they rely on their gut instinct in this scenario, they will be doing a lot of guesswork and will most likely fall victim to myths about process performance.
There are numerous tools available for determining what is wrong with a process. Ensuring that all processes, particularly those in the manufacturing industry, run smoothly is critical to achieving customer satisfaction and gaining a competitive advantage. This is essentially what process behaviour charts are for, which leads to the benefits mentioned above.
Read this article on 6sigma.com- https://6sigma.com/benefits-of-using-process-behavior-charts/