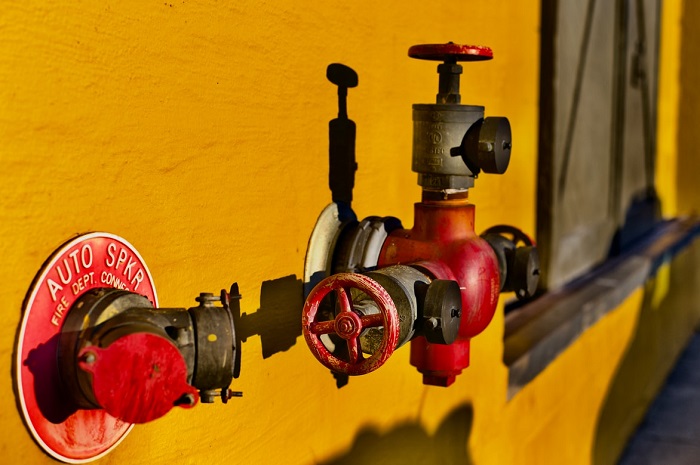
Globe valves are widely used in many industries; so much so that we often take them for granted, hardly thinking about them unless a problem occurs.
But because they are in such wide circulation, it’s important that engineers have a basic understanding of them, in case they are required to work on them at some stage. So this article covers 5 things every engineer should know about globe valves including;
- Identification - what they are and how they operate
- Differentiation - the various types in use
- Applications - the different roles they play
- Pros & cons - their advantages and disadvantages
- Maintenance – tips on their basic care and repair.
Identification
A globe valve is a linear motion valve employed in small size piping. It moves a disc into or out of its seat by means of a wheel and stem in order to start, stop or regulate flow.
It consists of the following parts;
- Wheel – turned to open or close the valve
- Yoke nut - internal threads cause the stem to rise or fall when the wheel is turned
- Bonnet - the top portion of the valve with an opening for the stem to pass through
- Stem - has the disc at one end and the wheel at the other
- Disc – moves into and out of the valve seat
- Seat – provides the seal when the disc is pressed against it.
Differentiation
There are a number of different types of globe valves, each designed to perform different duties. The most common body types are;
- Y-body - the seat and stem are at a 45° angle to the flow, providing a straighter flow path when fully opened. Often used with high pressures and other severe services.
- Z- body - a straight-through globe valve typically used for water applications with a Z-shaped diaphragm across the body containing the seat.
- Angle - the inlet and outlet are perpendicular. Used for transferring flow from vertical to horizontal, often in applications with periods of pulsating flow.
The most common bonnet types are;
- Screwed – cheaper due to its simple design
- Bolted - most popular, although it needs a gasket between the body and bonnet to prevent leakage
- Welded – lighter weight and popular in applications where no disassembly is required
- Pressure-seal – used for high pressure applications
- Flanged - can be designed for any size and operating pressure
- Union-ring – uses a screwed ring to attach the bonnet to the body.
The most common disc types are;
- Ball - conventional ball-shaped metal disc used for low-pressure services, primarily to start and stop flow
- Plug – tapered metal plug disc that seats into a cone, typically used for throttling services
- Composition – with an insert ring for a tighter closure, used in high temperature and pressure applications due to its resilience and erosion resistance.
Applications
Globe valves are used in a wide range of high and low pressure services including;
- Cooling water systems
- Fuel oil systems
- Control valve bypass systems
- High-point vents and low-point drains
- Oil and gas feedwater and chemical feeds
- Condenser air extraction and extraction drain systems
- Boiler and main steam vents and drains
- Turbine seals and drains.
Pros & cons
Globe valves are widely used because they offer tangible benefits such as;
- Top-entry access for easy maintenance
- Suitable for frequent opening and closing
- Can be kept open at any degree from full open to full close
- Very little lift is needed to attain full flow
- Angular models can change the direction of fluid flow
- Good throttling and shutoff capabilities
- Easy to maintain and resurface the seats
- Can be used in a wide range of temperature extremes
- Can be used for both gas and liquid systems.
Their main disadvantages include;
- More expensive due to complex design
- Not suitable for larger size piping
- High pressure drop
- Require greater force to seat the valve
- Heavier than other valves
- Not good for clean or sterile applications.
Maintenance
Globe valves should be regularly maintained to ensure leak-free operation. Some maintenance tips to keep in mind include:
- Gland packings must be replaced when they start to lose their properties.
- When replacing gland packings, coat the new packings liberally with grease.
- Do not over-tighten gland nuts to minimise leakage or you could distort the valve plates and break the stem.
- Regularly grease the threads and yoke nut, removing the old grease first.
- Make sure the gaskets used in the flanges are the correct size.
- Before installation, pressure-clean pipelines to prevent foreign bodies from falling into the valve.
- The flow direction is marked on the valve body and if not, the rule of the thumb is that the fluid will flow from below the valve seat/disc.
Hopefully, this guide has provided an insight into the basics of globe valves. If you’re an engineer who’s called on to work on them at some stage, recalling their different types, advantages and uses may help you to carry out a more effective inspection or repair.
And if you’re unsure, consulting the manufacturer or speaking with suppliers who are experts in their field is the best way to ensure compatibility in any application.