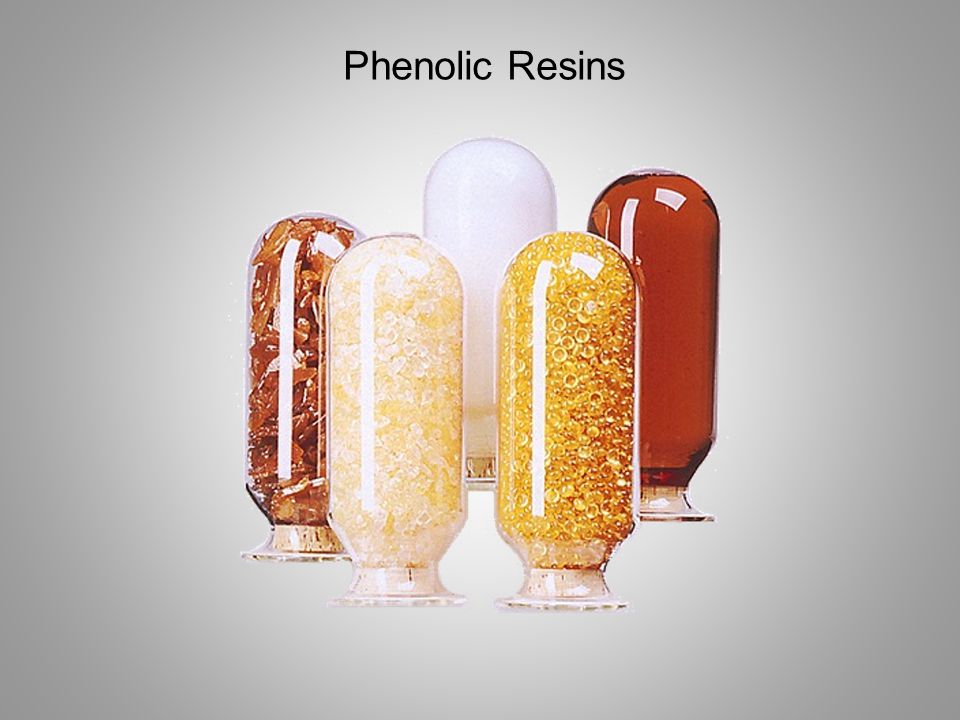
Polymers with high heat and electrical resistance are known as phenolic resins. It is mostly used to make moulding materials, abrasives, adhesives, laminates, friction materials, and insulators. Phenolic resins include Resol and Novolac. Resol is made under normal conditions with too much formaldehyde, whereas novolac is made under acidic conditions with too much phenol.
The primary application of phenolic resin is as a bonding agent. Phenolic resin easily penetrates and adheres to the structure of many organic and inorganic fillers and reinforcements, making it a good candidate for a variety of applications. The final properties are achieved after a brief thermal exposure to complete the cross-linking or "thermoset" process. The ability of phenolic resin to "wet out" and cross-link throughout the fillers and reinforcements aids in the engineering of the desired mechanical, thermal, and chemical resistance properties.
Properties
The ability to withstand heat, hardness, dimensional stability, electrical resistance, and chemical resistance are all notable properties of phenolic resin. Despite their durability, phenolic resins can be surprisingly brittle, which is why they are frequently combined with fillers and other reinforcements to strengthen the resin. Producers of phenolic resins divide the resin into two categories: novolac and resole. Novolac phenolic resins are catalysed in acid and require a curing agent, whereas resole resins are catalysed in alkali and do not require a curing agent.
Because some phenolic resins can withstand temperatures as high as 550 degrees Fahrenheit and are resistant to steam, phenolic moulding compounds, or PMCs, are frequently added to a variety of formulas to benefit from the final product's fire resistance. Glass fibre and specialty mould compounds that will be subjected to intense mechanical and thermal stress, such as pump impellers, are examples of this.
Phenolic resins are ideal for high-temperature applications where parts must adhere to fire safety regulations. Electronics, ballistics, mine ventilation, offshore water pipe systems, aerospace, rail, and mass transit are all applications for phenolic resins. Their key characteristics include low density (weight efficiency), low thermal conductivity, excellent corrosion and chemical resistance, a high strength-to-weight ratio, improved design flexibility, cost-effective production of complex 3D structures, excellent fatigue and impact properties, improved acoustic performance, radar/sonar transparency, and low maintenance.