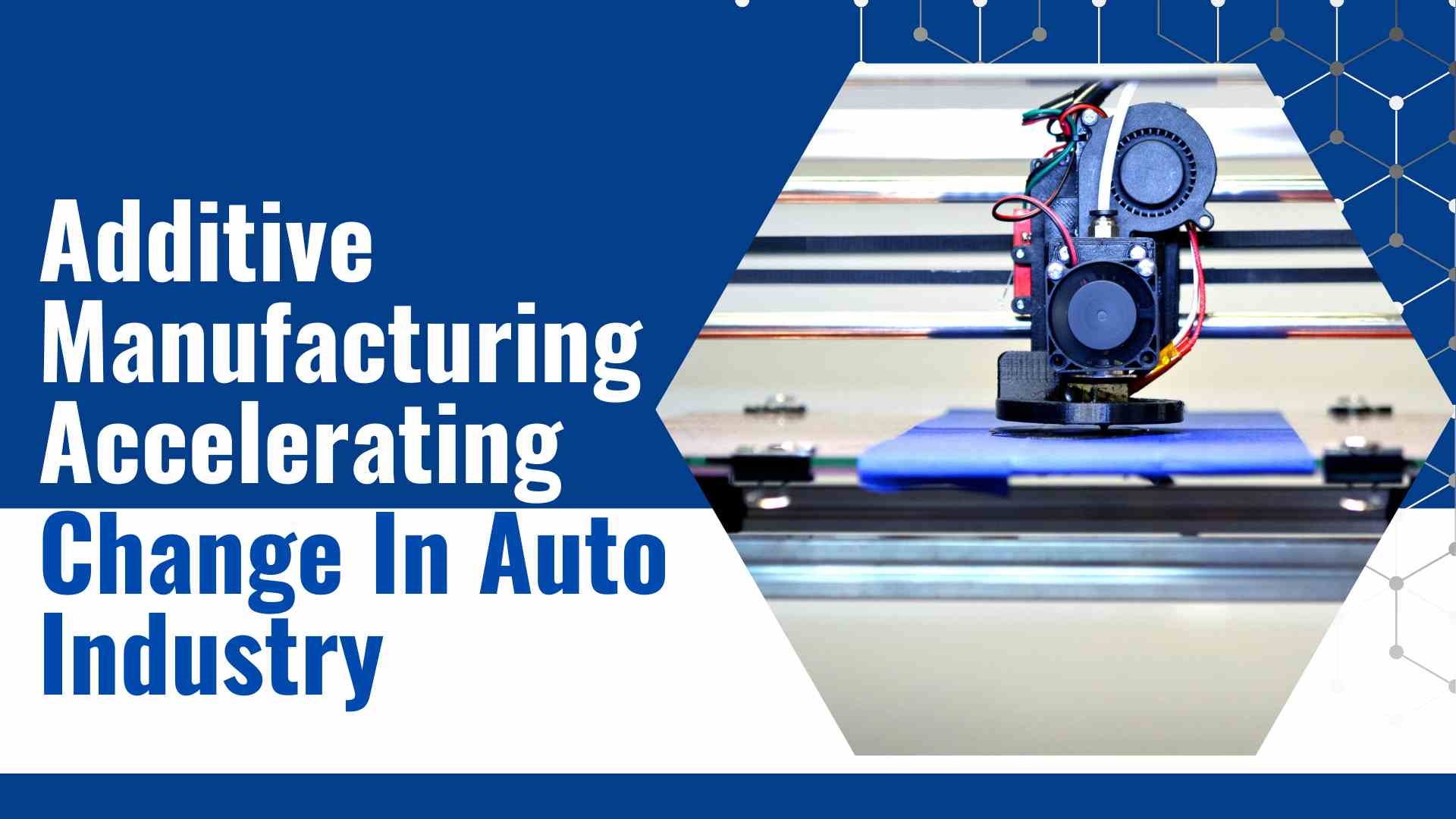
This article will talk about those areas and the role of metal powders and industrial gases in several Additive Manufacturing in the auto industry processes that involve laser metal fusion and laser metal deposition. It will also review how industrial gas technologies are helping to address the challenges ahead.
The popularity of additive manufacturing with powder metals has increased rapidly over the past five years. Because it offers several benefits, including shorter lead times, fewer process steps, less labor, and decreased waste. However, the potential of additive manufacturing in the auto industry is to produce new designs that are not possible with traditional metal fabrication methods such as casting and machining. With no demand for this tooling, parts can be manufactured faster and on-demand, decreasing the requirement for extensive machine infrastructure and inventory. Quality advances in powder metal processes supported by industrial gas technology are assisting to push additive manufacturing in the auto industry fast forward.
There is a logical industry evolution from prototyping to limited-scale production to mass production. Industrial gases such as nitrogen and argon and related control technology continue to help at each and every step. This involves improving the batch-to-batch quality of powder metals, the quality of metal 3D-printing processes, and completing operations.
Additive Manufacturing and Automotive
3D printing has been used previously in the automotive industry for prototyping for at least twenty years. Additive manufacturing is also now actively used in Formula 1 racing. Hence enabling teams to test different concepts in just a few weeks. So how will the automotive industry move additive manufacturing into mass production?
Additive manufacturing in the auto industry is already paving its path. There are signs that automotive manufacturers and suppliers are purchasing multiple machines to develop 3D-printing production capacity. Moreover, with a goal to fast-track rapid prototyping, tooling, and some pre-serial parts manufacturing. Incorporating multiple machines responds to one major drawback of additive manufacturing which is speed. Consequently, it may take 48 hours or more to produce a specialized metal part. But what if that part is required for 10,000 cars a year?
Ascending from simple prototyping to mass production is formidable for an entire passenger car. However, it is not a stretch for any single part. The simple answer is to 3D print 10,000 parts with the assistance of 55 to 60 printers. Advances in additive manufacturing technology, of course, can further progress 3D production rates. Also, when designing for manufacturing, a key target is to decrease assembly. A single additive manufacturing part can easily substitute several parts, directing to further improvements in production rates and reductions in assembly costs.
Pre-production Benefits
Fast-tracking the product design phase during new product development is important in any industry. Fortunately, 3D printing can replace expensive and long lead-time CNC production in this phase. Furthermore, precisely, it allows designers to cost-effectively go through various iterations before deciding on the final product. The process is as follows: once designers have found a user demand and have generated ideas to meet that demand, they create a prototype. The next stage is to test this prototype in order to enhance its design. This iterative process is also known as rapid prototyping.
Additive manufacturing in the auto industry plays a significant role. For example, Volkswagen has been working with additive manufacturing for the past 25 years. Also, it invested in two additional Stratasys 3D printers. In addition, tooling (jigs, grips, and fixtures) design can also be improved and produced at a lower cost. Tooling plays a considerable role on the assembly line to produce repeatable and high-quality products.
What is the Future of Automotive Additive Manufacturing Applications?
In the last few years, automakers have had to explore new business models to reach growth. Many looks towards new technologies, as well as additive manufacturing, to regulate short development cycles and to attain lower costs. Electric vehicles are also of interest, with about 50% of automotive manufacturers targeting to be market leaders in fully electric vehicles shortly. As the auto industry moves away from internal combustion engines, 3D printing rises as an answer that can elevate the development of lighter parts for electric vehicles. Certainly, light-weighting is important for electric vehicles as it directly impacts battery time.
Conclusion
The next 10 years will act as a game-changer for the automotive industry. The disruption of emerging trends and technologies including electrification, digitalization, driver assist, sustainability, and supply-chain agility can create new opportunities for AM. And thanks to constant innovation, we’re inching closer to scaling AM every day.
If you are also interested in taking an initiative in the information technology sector and looking for discussions with industry experts, then do not hesitate to contact us at Aeologic Technologies