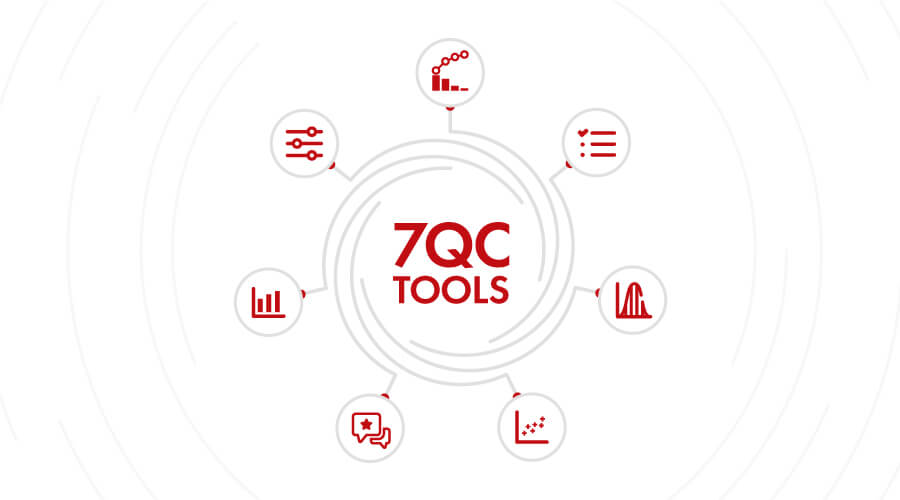
7 QC Tools For Quality Improvement With A Strategic Plan
Quality improvement process starts with knowing or identifying what and where the real problem is. The organization must know where they stand, what is the problem and the root cause of respective problem before recommending any solution for the improvement. Hence, locating and eliminating the root cause of the problem is one of the crucial parts of improvements. The 7 QC tools are most basic and easy to understand but most widely used for improvements and the 7QC tools training are imperative in the growth of a company.
The title—7QC—is given so because it provides a set of graphical techniques that are identified as most helpful in troubleshooting the existing issues. These are the fundamental instruments to improve quality and process. They are used systematically to understand and identify the risk, asses it, control fluctuations of product quality, and accordingly provide solutions to avoid future defects.
Benefits of 7 QC Tools
The 7 QC tools are structured and fundamental instruments that help businesses improve their management and production process for achieving enhanced product quality.
From assessing and examining the production process, identification of key challenges and problems to controlling the fluctuation present in the product quality and providing solutions for prevention of defects in future, the easy to understand and implement, 7 QC tools are very effective. Some of the major business benefits of 7 QC tools are listed below.
- Provides a more structured path for problem-solving and quality improvement
- Easy to understand as well as implement yet extremely effective
- A scientific and logical approach for problem-solving
- Follows the 80/20 rule i.e. gain 80% result with 20% efforts
- Improve the quality of product and services
- Helps in identifying and analyzing problems during the process
- Fishbone training aides in root cause analysis and problem-solving
- Encourages team spirit and fosters a healthy culture
- Identifies roots cause and solve it permanently
- Enhance customer experience and customer satisfaction
Based on the data-driven process and customer-centric approach, 7 QC tools implementation is one of the most effective processes that too in the shortest amount of time.
Cause and Effect Diagram
Cause and Effect Diagram also known as Fishbone Diagram helps in identifying the potential causes of an effect or a problem. In addition to sorting ideas in respective categories, it also helps in understanding the areas of opportunity through effective brainstorming. Fishbone training empowers you to identify the potential cause in the problem.
Control Chart
Control charts are used to study how the processes have changed over a period of time. Further, by comparing current data to historical control limits, one could lead to the conclusion about whether the process variation is consistent as in under control or unpredictable as in out of the control due to being affected by special causes of variation.
Pareto Chart
Pareto Chart is based on the 80/20 rule where it shows the significant factors that have the highest impact on the identified problem.
Check Sheet
Check sheet is a structured process which helps to collect and analyzing data. It is an effective tool that can be for a variety of purposes.
Histogram
Histogram is commonly used a graph that shows the data and its frequency of distribution to help users identify each different value in a set of data occurs.
Scatter Diagram
Scatter diagram shows the relationship between two important factors i.e. pairs of numerical data, one variable on each axis to demonstrate the relationship.
Stratification
Stratification also known as a flow chart or run chart is a technique that separates the data gathered from a variety of sources so that patterns can be seen i.e., the path an entity has taken through a defined process.
Utilizing the 7 QC tools in six sigma or quality management process helps in taking a systematic approach to identify and understand the risk, assess the risk, control fluctuation of product quality and accordingly provide solutions to avoid future defects.