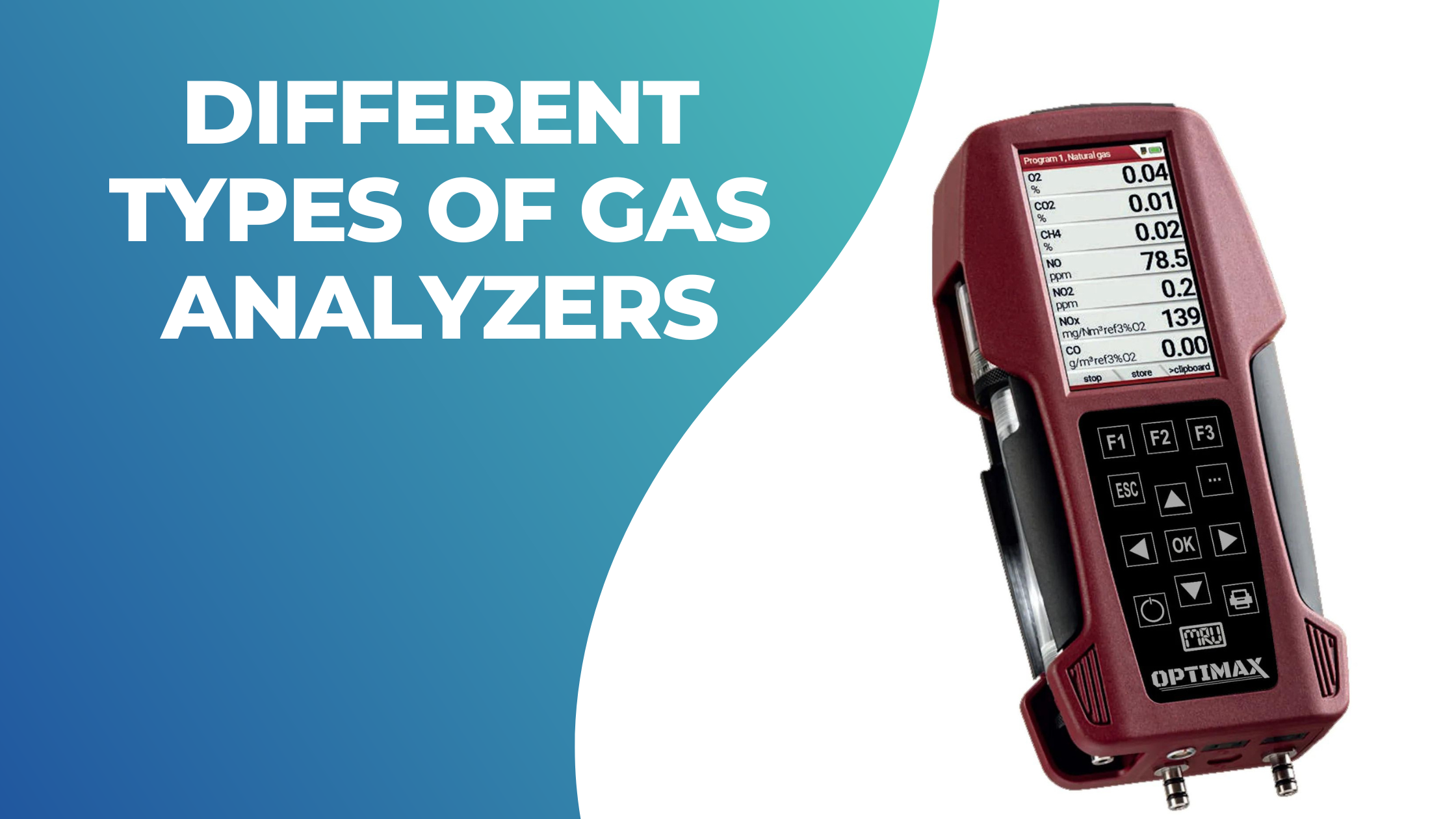
There are certain instruments that can accurately identify a huge number of gases in the atmosphere, but they are unable to differentiate between them. They are unable to determine the composition of those gases, hence figuring out their compositions requires a time-consuming analysis of each gas separately. Instruments like ampro 2000 gas analyzer take care of it for you. It not only recognises the various gases in the container but also provides information on their compositions, allowing you to distinguish between dangerous and non-hazardous gases.
When it comes to types, there are many different types of gas analyzers available in the market and each one of them has different functionalities than the other although the core functionality of detecting and analysing the gases remains the same.
Continuous Gas Analyzers
A substantial part of every mru analyzer product range consists of continuous gas analyzers. These kinds of equipment are often employed for facility-wide continuous gas analysis on a single sample point. These analyzers must have the proper sample conditioning components since they are designed to be permanently exposed to the sample gas. Since they are almost typically permanently affixed on a wall or other vertical surface, continuous analyzers are larger than portable analyzers.
Portable Gas Analyzers
The internal area that may be used for sample conditioning components is constrained by portable analyzers' compact size. This indicates that they lack the tools necessary to conduct lengthy analyses of complex sample gases. They are best suited for spot-checking and adjusting applications, though. The majority of portable gas analyzers contain some kind of condensate collecting and filter system. A sample could occasionally be too warm or damp, even for a quick examination. In this situation, a portable gas chiller is a wise choice.
Flue Gas Analyzers
In order to generate heat, fuel is burned in the presence of oxygen by furnaces, heaters, and boilers. The most efficient combustion and greatest cost savings may be achieved by achieving an intelligent balance of fuel and air. Optimising the amount of fuel and air input may be done very well by measuring the exhaust gas. You may use a flue gas analyzer to detect the concentrations of different gases and modify the burner settings on a boiler to assist ensure optimal combustion.
Hazardous Area Analyzers
Some gas analyzers made in cabinets are appropriate for use in hazardous areas. The cabinet itself is a large, mounting-footed box made of cast aluminium. The controls may be operated magnetically through a windowed cover with a threaded solid metal cover or vice versa. Flame/flash arrestors will be fitted at the analyzer's gas entrance and exit points, and wire entries must be shielded with an EYS seal that has been correctly installed.
Heat-Treating and Metal Finishing Analyzers
In steel finishing and heat treatment furnaces in steel mills, gas analyzers can be used to monitor atmospheric gases and flue gases. Typically, rolling mills, bar mills, blooming mills, wire mills, etc. are used to shape and finish molten steel after it has been created by the melt shop. These mills typically classify gas analysis as either flue gases or atmospheric gases. For safety reasons, many mills now mandate gas monitoring of the surrounding air around furnaces.
Landfill Gas Analyzers
Even though the gas itself is identical, analytical industry language usually divides biogas and landfill applications into two different groups. The varied waste input streams at landfill sites appear to have an average influence on the gas composition at each location. The gas is often highly caustic and aggressive. However, from the viewpoint of a gas analyzer, landfill applications are typically predictable and consistent enough to permit the specification of standard analytical apparatus.
Oil & Gas Industry Analyzers
For safe and effective operation, several petrochemical applications require oxygen analysis. The oil and gas (petrochemical) sector spans a wide range of processes and applications. Some of these may be generally divided into fundamental areas including research, development, production, distribution, and transportation. The majority of petrochemical sector applications involve tracking hydrocarbon or hydrocarbon and other gas combinations.
Portable Engine Exhaust Analyzers
Combustion engine exhaust gas analysis may be used to assess engine performance and identify issues. Oxygen (O2), Carbon Monoxide (CO), Carbon Dioxide (CO2), Nitrogen Oxide (NO), Nitrogen Dioxide (NO2), and Hydrocarbons (HCs) may all be measured with a mru ampro 2000 portable engine exhaust gas analyzer. The analyzer is often used in automobile exhaust gas analyzer applications and may be used to monitor engine exhaust emissions from 2 and 4 cycle engines driven by diesel, gasoline, propane, or natural gas.
Power Generation and Hydrogen Purity Analyzers
Due to the generally homogeneous nature of hydrogen uses in the power sector, standardised and high-quality gas analysis systems may be created. Heat is produced while current moves through a conductor. The same idea also applies to how much heat is produced when currents pass through the windings of an electric generator. Heat accumulation can lead to the deformation and lengthening of insulators and conductors, which could harm the generator.
Process Gas Analyzers
Gas analyzers of this category are used in a wide range of laboratory and light industrial process conditions. Process applications typically have minimal energy requirements and are not industrial in nature. The design of the analytical tools for these applications typically prioritises simplicity. The sample conditioning systems can be decreased due to the sample gas's cleanness and dryness. In some circumstances, we can add the examined gas back into the process if the detector's functioning and sample pressure gradient permit.
Steel-Making Analyzers
In steel mills and other heavy industries, gas analyzers can be used to monitor atmospheric and flue gases. The process of creating steel from iron ore, direct reduced iron products, and/or scrap is known as steelmaking. Modern steelmaking is mostly done in electric arc furnaces and basic oxygen furnaces. Steel waste and liquid pig iron from a blast furnace serve as the major inputs for the basic oxygen process. Direct reduced iron (DRI) or scrap steel are used as inputs in the electric arc furnace process.