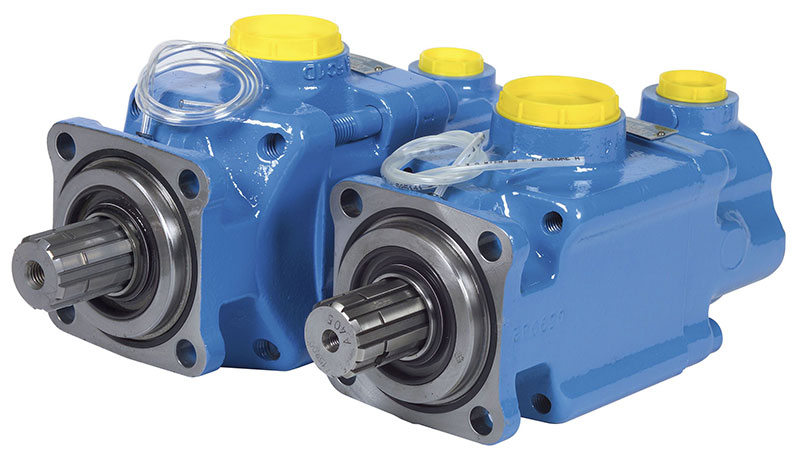
A gear pump is a type of positive displacement pump that uses meshing gears to pump fluids. It consists of two gears, a driving gear (the one connected to the motor) and a driven gear, both rotating in opposite directions inside a casing.
As the gears rotate, the fluid is trapped between the teeth of the gears and the pump casing, and is carried around the outside of the gears to the outlet port. The meshing of the gear teeth ensures that the fluid is displaced at a constant rate with each rotation of the gears, providing a smooth and steady flow.
Gear pumps are commonly used for low-to-medium pressure applications, and are ideal for pumping high viscosity fluids, such as oil, molasses, or chocolate. They are also commonly used in hydraulic systems and fuel delivery systems.
There are two types of gear pumps: external and internal. External gear pumps have two gears of the same size, and the fluid flows between the gears and the casing. Internal gear pumps have a larger driving gear and a smaller driven gear, and the fluid flows between the gears.
Some advantages of gear pumps include their simplicity, reliability, and durability, as they have few moving parts and can handle a wide range of fluids. However, they are not suitable for high-pressure applications or for pumping abrasive fluids, as the gear teeth can wear over time.
20 benefits of hydraulic gear pumps
Here are 20 benefits of hydraulic gear pumps:
- High efficiency: Hydraulic gear pumps are highly efficient, providing a high flow rate with minimal energy loss.
- Compact size: Gear pumps are relatively small and lightweight, making them easy to install and operate.
- Low cost: Compared to other types of hydraulic pumps, gear pumps are generally less expensive, making them a cost-effective choice for many applications.
- High pressure capability: Some types of gear pumps can operate at high pressure, making them suitable for demanding applications.
- Low noise: Gear pumps operate quietly, making them a good choice for applications where noise is a concern.
- High reliability: Gear pumps are simple in design and have few moving parts, making them highly reliable.
- Easy maintenance: Gear pumps are easy to maintain and repair, with replacement parts readily available.
- Good resistance to wear: The design of gear pumps allows for good resistance to wear, even in harsh operating conditions.
- Easy to control: Gear pumps are easy to control, with simple on/off or variable speed control options.
- Wide range of flow rates: Gear pumps are available in a wide range of flow rates, making them suitable for a variety of applications.
- Good accuracy: Gear pumps provide good accuracy in flow rate and pressure, making them suitable for precision applications.
- Minimal pulsation: Gear pumps provide a smooth flow of hydraulic fluid with minimal pulsation, reducing the risk of damage to hydraulic components.
- High volumetric efficiency: Gear pumps provide a high volumetric efficiency, meaning that they can deliver a high flow rate with minimal internal leakage.
- Good suction capability: Gear pumps have good suction capability, meaning that they can draw in fluid even from a low supply pressure.
- Self-priming: Some types of gear pumps are self-priming, meaning that they can draw in fluid without the need for external priming.
- High temperature capability: Gear pumps can operate at high temperatures, making them suitable for high-temperature applications.
- Good chemical resistance: Gear pumps are available in materials that provide good resistance to various chemicals, making them suitable for a range of industrial applications.
- Flexible mounting options: Gear pumps can be mounted in various orientations and in tight spaces, providing flexibility in installation.
- Versatile: Gear pumps can be used in a wide range of applications, including in the automotive, construction, agriculture, and marine industries.
- Low friction: The design of gear pumps results in low friction between the moving parts, reducing wear and energy loss.
20 tips for buy gear pumps
- Determine your flow rate needs: Before buying gear pumps, it's essential to determine your flow rate requirements.
- Know the fluid characteristics: It's important to know the fluid characteristics such as viscosity, temperature, and chemical compatibility with the pump material.
- Choose the right pump material: Different pump materials are suitable for different fluids, so choose the one that is compatible with the fluid you're pumping.
- Consider the pressure requirements: Make sure the pump can handle the required pressure for your application.
- Determine the inlet and outlet sizes: Choose the pump with the appropriate inlet and outlet sizes to fit your system.
- Check for cavitation: Make sure the pump is designed to prevent cavitation, as it can damage the pump.
- Look for self-priming options: A self-priming pump is a convenient option for applications where the pump is not always full of fluid.
- Check the motor requirements: Make sure the pump is compatible with the motor you plan to use.
- Consider the noise level: Look for a pump that produces minimal noise if it's going to be used in a noise-sensitive environment.
- Check for vibration: Look for a pump with low vibration to reduce wear and tear on the system.
- Choose the right pump size: Choose the pump size that is appropriate for your flow rate needs.
- Look for energy-efficient options: Choose a pump that is energy-efficient to reduce operating costs.
- Consider maintenance requirements: Choose a pump that is easy to maintain to reduce downtime and repair costs.
- Check the warranty: Look for a pump with a good warranty to ensure that you are covered if any issues arise.
- Look for certification: Look for pumps that are certified to meet industry standards.
- Consider the manufacturer's reputation: Choose a pump from a reputable manufacturer with a good track record.
- Check for availability of spare parts: Make sure that spare parts are readily available for the pump you choose.
- Check for ease of installation: Choose a pump that is easy to install to reduce installation costs.
- Look for accessories: Look for pumps that come with accessories such as valves and gauges to reduce additional costs.
- Read reviews: Read reviews from other customers to get an idea of the pump's performance and reliability.
gear pump types
There are different types of gear pumps available in the market, and each has its own advantages and disadvantages.
Here's a comparison of some common types of gear pumps:
External Gear Pumps: This type of gear pump has two external gears that rotate to create suction and discharge pressure. They are simple in design, easy to maintain, and can handle high pressures. However, they are prone to leakage and may not be suitable for high viscosity fluids.
Internal Gear Pumps: This type of gear pump has one external gear and one internal gear that mesh together to create suction and discharge pressure. They are efficient, can handle high viscosity fluids, and are less prone to leakage. However, they are more complex in design and may be more expensive.
Gerotor Pumps: This type of gear pump has an outer rotor with internal teeth and an inner rotor with external teeth that mesh together to create suction and discharge pressure. They are compact in size, efficient, and can handle high viscosity fluids. However, they are more expensive and may not be suitable for high-pressure applications.
Lobe Pumps: This type of gear pump has two lobes that rotate to create suction and discharge pressure. They are efficient, can handle high viscosity fluids, and are less prone to pulsation. However, they may be more expensive, and the lobes may wear down quickly.
Peristaltic Pumps: This type of gear pump uses a flexible tube and rollers to create suction and discharge pressure. They are suitable for handling abrasive and shear-sensitive fluids, but they may have limited flow rates and may be more prone to wear and tear.
In summary, external gear pumps are simple and easy to maintain, while internal gear pumps are efficient and can handle high viscosity fluids. Gerotor pumps are compact and efficient, lobe pumps are suitable for high viscosity fluids, and peristaltic pumps are ideal for handling abrasive and shear-sensitive fluids. Choosing the right type of gear pump depends on your specific application and fluid requirements.