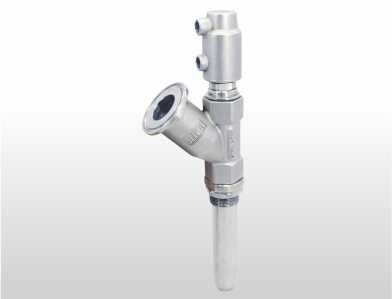
Control valves are an essential component of many industrial processes, allowing for precise control of fluid flow rates and pressures. In this comprehensive guide, we'll explore the function, types, and applications of control valves in detail.
What is a Control Valve?
A control valve is a device that regulates the flow of fluid, typically a liquid or gas, through a pipeline or other system. It accomplishes this by altering the size of the opening through which the fluid passes, thereby changing the flow rate and pressure. Control valves are commonly used in industrial applications such as oil and gas production, chemical processing, and power generation.
Types of Control Valves
There are several types of control valves, each with its own unique design and function. Some of the most common types include:
Globe valves: Globe valves are a popular choice for regulating flow in industrial applications. They feature a spherical body with an internal baffle that directs the fluid flow through the valve.
Ball valves: Ball valves use a ball-shaped disc to regulate flow. When the valve is open, the ball is rotated to allow fluid to pass through, and when it is closed, the ball is rotated to block the flow.
Butterfly valves: Butterfly valves use a disc-shaped component with a pivot in the center to regulate flow. When the valve is open, the disc is rotated to allow fluid to pass through, and when it is closed, the disc is rotated to block the flow.
Diaphragm valves: Diaphragm valves use a flexible diaphragm to regulate flow. When the valve is open, the diaphragm is lifted to allow fluid to pass through, and when it is closed, the diaphragm is lowered to block the flow.
How do Control Valves Work?
Control valve work by using a combination of mechanical and electrical components to regulate fluid flow. The valve body, which houses the moving components, is connected to the pipeline or system through which the fluid is flowing. Inside the valve body, there is a component called the trim, which controls the size of the opening through which the fluid passes.
The trim is typically composed of a valve plug, which moves up and down to control the opening size, and a valve seat, which provides a seal around the plug. When the plug is moved up, the opening size increases, allowing more fluid to pass through. When the plug is moved down, the opening size decreases, restricting the flow of fluid.
Control valves can be operated manually or automatically, depending on the application. Manual control valves are adjusted by hand, while automatic valves use electrical or pneumatic signals to adjust the valve position.
Applications of Control Valves
Control valves are employed in a variety of manufacturing processes, such as:
Oil and gas production: Control valves are used to regulate the flow of oil and gas in pipelines and production facilities.
Chemical processing: Control valves are used to control the flow of chemicals in chemical plants and refineries.
Power generation: Control valves are used to regulate the flow of steam and other fluids in power generation facilities.
Water treatment: Control valves are used to control the flow of water in treatment plants and distribution systems.
In conclusion, control valves are an essential component of many industrial processes, providing precise control over fluid flow rates and pressures. By understanding the function, types, and applications of control valves, you can make informed decisions when selecting and operating these critical components. It is important to select the right type of control valve for the specific application to ensure optimal performance and efficiency.
When selecting a control valve, factors such as the fluid type, flow rate, pressure, temperature, and required accuracy must be considered. In addition, the operating environment, including the presence of corrosive or abrasive materials, must also be taken into account.
Regular maintenance and testing of control valves are also important to ensure optimal performance and avoid costly downtime. This includes inspecting the valve for leaks, checking the positioner and actuator for proper operation, and replacing any worn or damaged components.
In summary, control valves are a critical component of many industrial processes, allowing for precise control of fluid flow rates and pressures. Understanding the function, types, and applications of control valves is essential for selecting and operating these components effectively. Proper selection, operation, and maintenance of control valves can help improve efficiency, reduce downtime, and ensure the safety and reliability of industrial processes.