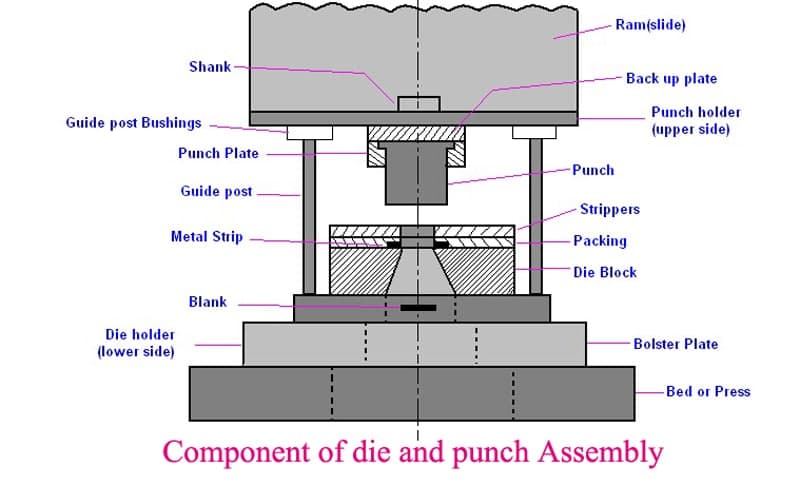
In the world of precision manufacturing, every little detail matters. From intricate metal components to delicate parts for electronics, achieving accurate and consistent results is paramount. One critical factor that plays a significant role in precision manufacturing is "Die Punch Clearance." In this blog, we will delve into the concept of clearance, its importance, how it affects manufacturing processes, and best practices for achieving optimal results.
What is Die Punch Clearance?
Die punch clearance refers to the space or gap between the punch (male part) and the die (female part) in a metal forming process. In manufacturing, a punch and die are used to shape and cut materials such as metal sheets, plastics, and other workpieces. The clearance between the punch and die ensures that the material flows smoothly and evenly during the forming process.
The Importance of Die Punch Clearance:
Achieving the right clearance is crucial for several reasons:
● Material Flow and Quality: The proper clearance allows for smooth material flow between the punch and die, preventing any sticking or dragging. This ensures consistent quality and reduces the chances of defects in the final product.
● Tool Life: In precision manufacturing, tool life is of utmost importance. An incorrect clearance can lead to excessive wear and tear on the punch and die, shortening their lifespan and increasing production costs.
● Dimensional Accuracy: Accurate and consistent punch clearance helps maintain the dimensional accuracy of the final product. Any deviation in clearance can result in variations in the finished parts, leading to assembly issues or product failure.
● Burr Formation: Inadequate punch clearance can cause burr formation during the forming process. Burrs are unwanted raised edges or rough surfaces that affect the part's functionality and aesthetics.
● Productivity and Efficiency: Proper die & punch clearance contributes to smoother manufacturing processes, reducing the need for rework or corrections, and ultimately increasing productivity and efficiency.
Factors Affecting Die & Punch Clearance
Several factors influence the determination of the appropriate die punch clearance for a specific manufacturing process:
● Material Type and Thickness: Different materials and their thicknesses require varying clearance values. Harder materials might need larger clearances to accommodate spring-back, while softer materials may require smaller clearances to avoid deformation.
● Punch and Die Material: The material of the punch and die also affects the clearance. The hardness and surface finish of these components can impact friction and wear during the forming process.
● Workpiece Geometry: The shape and complexity of the workpiece play a role in defining the required clearance. Complex shapes may necessitate larger clearances to allow for material flow and reduce stress concentration.
● Forming Process: The type of forming process, such as bending, blanking, or deep drawing, influences the appropriate die & punch clearance. Each process has its own specific requirements for optimal results.
Determining the Right Die Punch Clearance
Achieving the perfect die punch clearance requires a combination of experience, testing, and analysis. Here are some guidelines to help manufacturers determine the optimal clearance:
● Material Testing: Conducting tests with different clearance values on sample materials can provide insights into the appropriate clearance required for a specific material.
● Simulation Software: Advanced simulation software can be utilized to model the forming process and predict the behavior of the material under various clearance settings.
● Past Experience: Leveraging past experience in similar manufacturing processes can be valuable in estimating initial clearance values.
● Industry Standards and Guidelines: Referring to industry-specific standards and guidelines can offer valuable starting points for die & punch clearance values.
Best Practices for Punch Die Clearance
To ensure the best results and streamline the manufacturing process, manufacturers should follow these best practices:
● Regular Maintenance: Regularly inspect and maintain the punch and die to prevent excessive wear and ensure consistent results.
● Documented Processes: Document the die & punch clearance values used for each manufacturing process to maintain consistency and aid in troubleshooting.
● Collaboration between Design and Manufacturing Teams: Effective communication between design and manufacturing teams helps ensure that the intended clearance values are incorporated into the product design.
● Adaptation to Material and Process Changes: As materials and processes evolve, it's essential to reevaluate and adjust clearance values accordingly.
The Impact of Die Punch Clearance on Product Quality
Proper die punch clearance significantly influences the quality of the final product. A well-maintained clearance ensures that the material flows smoothly during the forming process, minimizing the chances of defects and surface imperfections. When the clearance is too tight, it can cause drag and excessive stress on the material, leading to cracks, deformations, or even material tearing. On the other hand, too much clearance may result in a loss of dimensional accuracy and increased burr formation.
Extending Tool Life through Optimal Die Punch Clearance
In precision manufacturing, tool life directly affects production costs and overall efficiency. Die & punch clearance play a crucial role in prolonging the lifespan of punches and dies. With the appropriate clearance, friction and wear between the punch and die are minimized, reducing the risk of premature tool failure. Manufacturers can achieve cost savings by avoiding frequent replacements and downtime for tool maintenance.
Advancements in Die & Punch Clearance Techniques
As technology continues to advance, the manufacturing industry continuously seeks innovative solutions to enhance precision and efficiency. Simulation software and computer-aided design (CAD) tools have become instrumental in predicting material behavior and optimizing die & punch clearance values. Manufacturers can now simulate the forming process, test various clearance settings, and visualize potential issues before starting physical production.
Conclusion
Die punch clearance is a critical factor in precision manufacturing that directly impacts product quality, tool life, and overall productivity. By understanding its significance and implementing best practices, manufacturers can achieve consistent and accurate results in their forming processes. The right die & punch clearance ensures smooth material flow, and dimensional accuracy, and minimizes defects, ultimately contributing to the success of precision manufacturing industries. As technology advances and materials continue to evolve, die & punch clearance will remain an essential aspect of the manufacturing world, shaping the future of precision engineering.