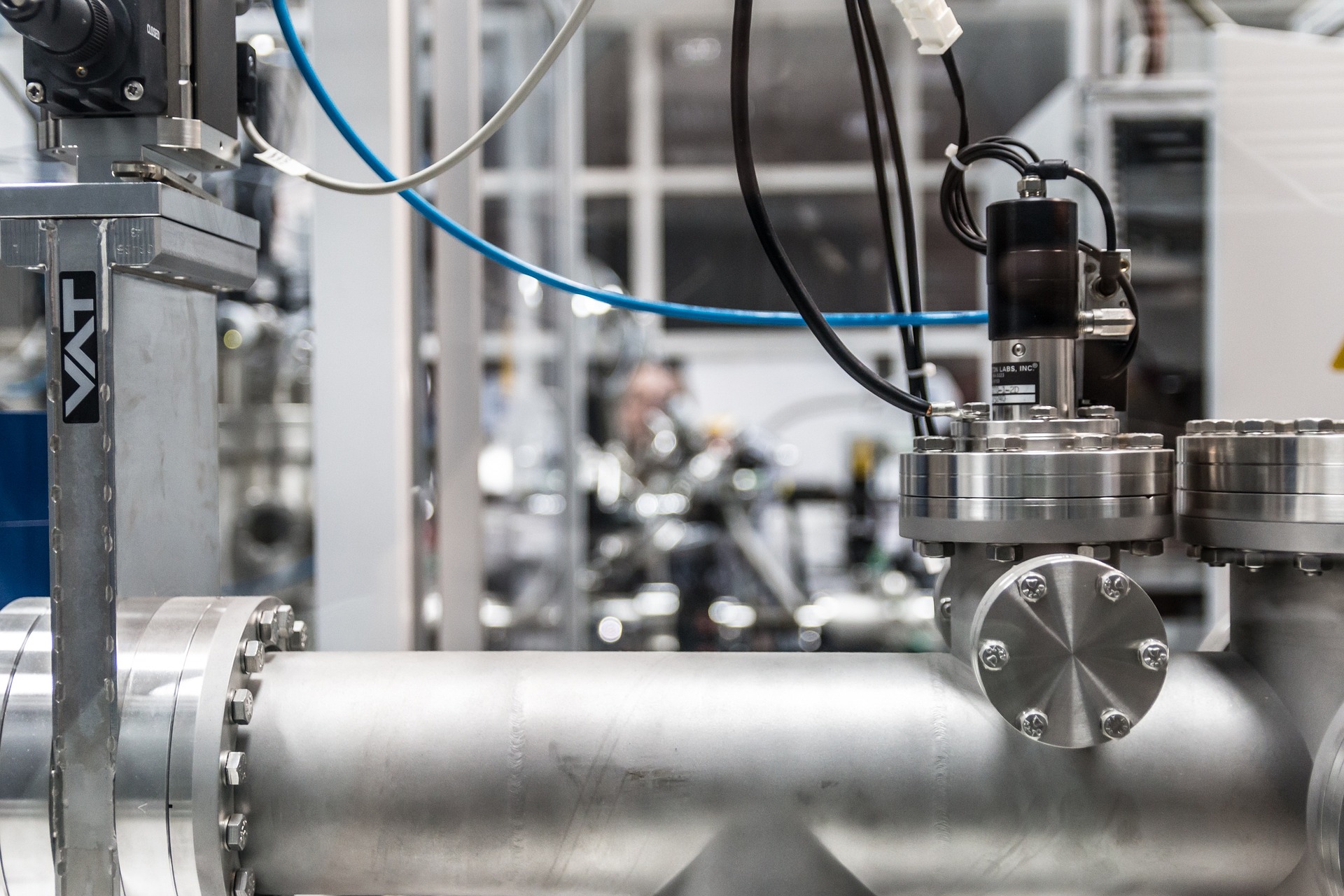
In the ever-evolving world of manufacturing, precision and efficiency are paramount. One of the key technologies that has revolutionized the way products are made is plastic injection mould tooling. This process, which may seem like a well-kept secret to many, plays a crucial role in bringing a wide range of plastic products to life.
In this article, we will explore the fascinating world of plastic injection mould tooling, its applications, and how it has become an indispensable part of the manufacturing process.
Understanding The Basics Of Plastic Injection Mould Tooling
Before delving into the intricacies of plastic injection mould tooling, let's break down the basics.
At its core, this technique involves the creation of precise and intricate plastic components by injecting molten plastic material into a carefully crafted mould. This mould, known as the tool or die, serves as the negative of the desired part. Once the molten plastic cools and solidifies inside the mould, it is ejected to reveal the final product.
Designing The Perfect Mould
Creating a mould is an art in itself. Manufacturers must take into account the product's design, size, and intricacies when crafting the mould.
The process starts with CAD (Computer-Aided Design) software, where engineers meticulously design the mould, considering every aspect, from the part's shape to the gate and runner system.
The gate is the entry point for the molten plastic, while the runner system ensures uniform distribution of the material within the mould.
Material Matters
The choice of material for the mould is critical. Typically, moulds are made from high-strength steel alloys, such as hardened tool steel, to withstand the high pressures and temperatures involved in the injection process.
The selection of the right material ensures the longevity and durability of the mould, allowing it to produce thousands - or even millions - of parts with minimal wear and tear.
The Injection Moulding Process
Once the mould is ready, it's time to bring it to life.
The injection moulding process begins with the heating of plastic resin pellets to their melting point. This molten plastic is then forced into the mould cavity under high pressure, filling every nook and cranny of the mould. As the plastic cools and solidifies, the mould opens, revealing the newly formed part.
This entire cycle can happen in a matter of seconds, making injection moulding one of the fastest and most efficient manufacturing processes available.
Applications Across Industries
The versatility of plastic injection moulding is truly astonishing. It finds applications in a wide range of industries, from automotive and aerospace to medical devices and consumer goods.
Let's explore a few key sectors where plastic injection mould tooling is instrumental:
1. Automotive Industry: From interior components like dashboard panels to exterior parts like bumpers, the automotive industry relies heavily on injection moulded plastics. These parts need to meet strict safety and durability standards, and plastic injection moulding is up to the task.
2. Medical Devices: The precision and repeatability of injection moulding make it ideal for producing intricate medical devices, such as syringes, surgical instruments, and even implantable components. The use of sterile materials and precise manufacturing processes is paramount in this industry, and plastic injection moulding delivers on both fronts.
3. Consumer Electronics: In the fast-paced world of consumer electronics, manufacturers must produce sleek and lightweight components. Injection moulding allows for the mass production of intricate, high-quality plastic parts used in smartphones, laptops, and other devices.
4. Packaging: Think of all the plastic containers and packaging materials you encounter daily. From food containers to beverage bottles, plastic injection moulding plays a pivotal role in creating these essential items quickly and efficiently.
Sustainability And Plastic Injection Moulding
In an era where sustainability is a top concern, it's crucial to address the environmental aspects of plastic injection moulding. While plastic is a versatile and durable material, its disposal can be a challenge.
However, manufacturers are taking steps to mitigate this issue by using some of the following measures:
1. Recycling: Many plastic injection moulded products can be recycled, reducing the strain on natural resources. Manufacturers are increasingly using recycled plastics in the moulding process to create eco-friendly products.
2. Energy Efficiency: Modern injection moulding machines are designed to be energy-efficient, minimizing the environmental impact of production. They use advanced technologies to optimize the heating and cooling processes, reducing energy consumption.
3. Design For Sustainability: Engineers and designers are now focusing on creating products that use less plastic while maintaining their functionality and durability. This approach, known as ‘design for sustainability’, aims to reduce the overall environmental footprint of plastic products.
Moulding The Modern World
Plastic injection mould tooling has undoubtedly transformed the landscape of manufacturing.
Its precision, speed, and versatility have made it a cornerstone of numerous industries. From intricate medical devices to everyday consumer goods, plastic injection moulding has left its mark. Moreover, with a growing emphasis on sustainability, the industry is adapting to minimize its environmental impact.
As technology continues to advance, plastic injection mould tooling is likely to evolve further, enabling manufacturers to produce even more complex and sustainable products. This remarkable process, born from ingenuity and engineering prowess, reminds us that the art of manufacturing is ever-evolving, always pushing the boundaries of what is possible.