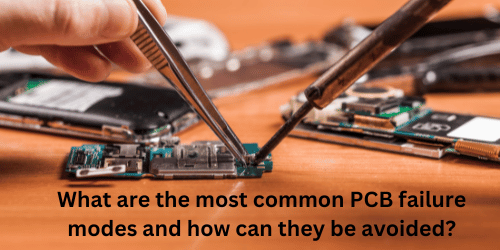
PCBs are at the heart of today’s technological landscape, supplying power to electronic devices and systems that have become necessary in our daily lives. Their importance spans technological advancements, streamlined production, customization, and the continuous evolution of electronics in a hyper-connected world.
PCBs are the building blocks of nearly all electronic gadgets we use every day, including smartphones, computers, tablets, televisions, cameras, smartwatches, and others. These gadgets rely on printed circuit boards (PCBs) to connect and power the electronic components that enable them to function.
Quality materials must be used in PCB design to provide a high level of reliability, performance, and functionality. It assures that the PCB satisfies design criteria, performs consistently over time, and is resistant to a variety of environmental and mechanical problems.
Understanding PCB design the Causes of PCB Failure and Troubleshooting
PCB failure is the condition that occurs when a Printed Circuit Board (PCB) malfunctions or ceases to perform as intended. A variety of circumstances can lead to PCB failure, which in turn can cause the electronic device or system that uses the PCB to malfunction. PCB failure can emerge in a variety of ways, depending on the source and severity of the problem.
PCB Failure Modes: Common Causes:
Circuit board diagnostics are crucial in determining the root cause of PCB failure. When a PCB fails or stops working, diagnostic procedures are utilized to identify the defective components or sections of the board. PCB (Printed Circuit Board) failure can occur for a variety of reasons, and these failures can be classified into distinct modes depending on the underlying cause.
- Soldering Defects: Poor soldering of components onto the PCB, such as cold solder joints or solder bridges, can cause connection difficulties and occasional failures.
- Component Failure: Electronic components, such as resistors, capacitors, and integrated circuits, can fail as a result of manufacturing flaws, aging, or external causes such as voltage spikes or overheating.
- Environmental Factors: Prolonged exposure to adverse environmental conditions such as high temperatures, humidity, dust, or corrosive substances can cause PCB materials to decay or electronic components to fail.
- Mechanical Stress: Bending, vibration, or shock, for example, might induce mechanical failure of solder junctions or fractures in the PCB, resulting in connectivity issues.
- Electrical Overload: If PCBs are subjected to excessive electrical current or voltage over their design limits, they can fail, resulting in burnouts or damage to electronic components.
- Design Errors: Inadequate PCB design, such as faulty trace routing, insufficient trace widths, or insufficient clearance between traces, can result in performance difficulties or short circuits.
- EMI/EMC Interference: Electromagnetic interference (EMI) or electromagnetic compatibility (EMC) concerns can cause signal interference and result in erratic behavior or breakdowns.
PCB troubleshooting frequently necessitates an elimination process as well as numerous testing methods such as visual examination, electrical testing, thermal testing, and X-ray analysis. Once the root cause of the failure has been determined, the PCB can be fixed or replaced to restore functioning.
The Effects of PCB Failure on Industries
Failure of a PCB (Printed Circuit Board) can have serious consequences for industries, affecting different areas of operations, productivity, and financial performance. Some of the most significant effects of PCB failure on industries include:
- Downtime and Production Loss: PCB failures in important industrial systems can cause unscheduled downtime, interrupting manufacturing processes. As a result, the company’s productivity and revenue suffer.
- Increased Maintenance and Repair Costs: When a PCB fails, repairs or replacements are required, which can be expensive, especially if the PCBs are complex or require specialized components. Increased maintenance expenses can have an impact on industry profitability.
- Supply Chain interruptions: When important components or systems in the supply chain fail, it can cause interruptions and delays in product deliveries, reducing overall supply chain efficiency.
- Product Recalls and Reputational Damage: Where PCB failures constitute a safety issue or affect a large number of products, manufacturers may be forced to conduct costly product recalls. This can result in reputational harm and a loss of consumer trust.
- Waste and Environmental Impact: Failed PCBs can contribute to electronic garbage (e-waste) if they are not properly recycled or disposed of. Improper e-waste handling can have a negative impact on the environment.
- Worries about Product Reliability and Safety: Industries that rely on electronic systems with PCB failures may have worries about the reliability and safety of their goods or processes. This can result in lost customer trust and significant liability issues.
- Competitive Disadvantage: Industries that suffer from frequent PCB failures may be at a competitive disadvantage when compared to competitors that have more reliable products and systems.
- Reduced Operational Efficiency: PCB failures can interrupt operations and workflows, resulting in decreased operational efficiency and longer completion times.
How Can You Prevent PCB Design Failure During PCB Assembly?
To avoid PCB failure during PCB assembly, pay close attention to the entire design and manufacturing process. Here are some critical actions and considerations for avoiding PCB failure:
- Quality Materials: High-quality PCB materials that are appropriate for the application and operational environment should be used. Choose materials with good heat conductivity, electrical characteristics, and environmental resilience.
- Design Verification: Before proceeding to the manufacturing stage, perform extensive design verification and testing. Check for potential issues such as signal integrity concerns, heat hotspots, and clearance violations using simulation tools.
- DFM (Design for Manufacturability): Design the PCB with production in mind. Ascertain that the design is appropriate for efficient assembly procedures, and avoid complex layouts that may result in faults.
- Correct Component Selection: Select dependable and appropriate components for the application. Check to make sure the components can withstand the expected voltage, current, and climatic conditions.
- Quality of Soldering and Assembly: Use high-quality soldering methods and tools. When possible, use automated assembly methods to limit the chance of human error.
- Thermal Management: To avoid overheating, use appropriate thermal management solutions. To properly dissipate heat, use heat sinks, thermal vias, and optimum component positioning.
- Soldering and Assembly Quality: Consider conformal coatings or encapsulation to shield the PCB from moisture, dust, and other environmental conditions.
- Electromagnetic Compatibility (EMC): To reduce the danger of interference and signal disruptions, ensure that the PCB design adheres to electromagnetic compatibility standards.
- Testing and Inspection: At various phases of the manufacturing process, do extensive testing and inspection. In-circuit testing (ICT), functional testing, and visual inspection are all included.
- Handling and Storage of Components: Handle and store components properly to avoid damage from electrostatic discharge (ESD) or exposure to environmental risks.
- Corrective Actions: Analyze any previous failures or faults to determine root causes and implement corrective actions to avoid repeating the same mistakes.
- Iterative Improvement and Prototyping: Before full-scale production, prototype the PCB design and test it in real-world situations. Iterative improvement can be used to fine-tune the design and address any difficulties that come up during prototyping.
- Regular Maintenance and Monitoring: Implement regular maintenance and monitoring procedures for deployed systems to discover and fix any issues before they cause failure.
PCB assemblers can considerably reduce the likelihood of PCB failure, and diagnosis, and ensure that electronic devices and systems work consistently and effectively over their intended lifetimes by following these procedures.