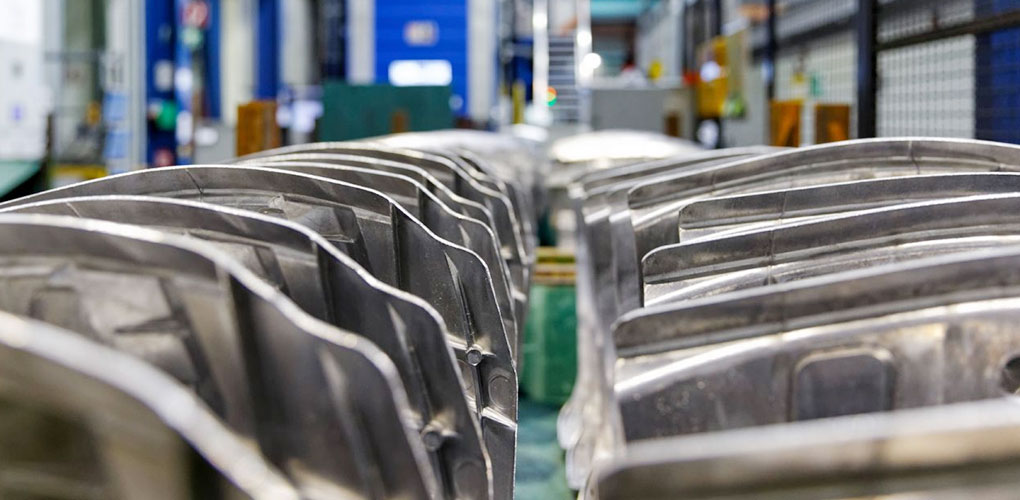
The effect of rare earth alloys on the microstructure and properties of zinc alloy die-casting was studied by modifying zinc alloy die-casting. This allowed for the study of the effect of rare earth alloys. The findings are presented above. At the same time, the function of rare earth alloy elements was investigated and discussed. This revealed an efficient method for further enhancing the mechanical properties of die-cast zinc alloys as well as their resistance to intergranular corrosion.
Intergranular corrosion is the most common flaw found in traditional die-cast zinc alloys and is the primary factor contributing to the low quality of the finished product. Because of this, manufacturers all over the world lost foam casting, including Yuge, use zinc that is high in purity and low in impurities, and they strictly control the chemical composition of die-cast zinc alloys. This is done in order to reduce the risk of intergranular corrosion.
To this end, the experiment focuses on the impact of rare earth modification treatment on the metallographic structure and mechanical properties of die-cast zinc alloys. The goals of this experiment are to obtain a new die-cast zinc alloy with improved performance and greater adaptability, and at the same time, to provide a reference for the addition of rare earths to die-cast zinc alloys. Procedure for testing
The following materials were used in the experiment: a No. 1 zinc ingot, a No. 1 electrolytic copper ingot, and a No. 1 nickel ingot. The graphite crucible and a 45 kW crucible resistance furnace are the pieces of smelting equipment lost foam casting that were used for the test. The experiment uses a die-cast zinc alloy called ZnAl4-1 (Al3.2% Cu0.73% 1.25%, Mg0.06%, and the rest is Zn), to which an appropriate amount of rare earth alloys has been added. The goal of the experiment is to study how the addition of rare earth alloys affects the metallographic structure and mechanical properties of alloys. Copper and rare earth elements are combined to form master alloys and added to the material.
The procedure for smelting is as follows: first, heat the graphite crucible until it turns a dark red color; then, put aluminum ingots and aluminum-copper master alloy into the crucible; then, wait until some of the aluminum liquid appears in the crucible; finally, add a covering agent that accounts for approximately 2% of the total weight of the charge. The covering agent is made up of NaCl at a concentration of 40%, KCl at a level of 20%, and Na3AlF at a level of 60%. The percentage of the charge's total weight that is comprised of C2Cl6 is 0.3%. The melting point of the liquid is 550 degrees Celsius. Die casting can be done with the zinc alloy ingots after they have been poured. The effects of rare earths on the microscopic box phase structure of die-cast zinc alloy, as determined by testing and analysis
1) Impact on the structure after casting
Hypoeutectic alloys consist of die-cast zinc alloys that contain approximately 4% aluminum. In comparison to the ZnAl4-1 alloy that has not been subjected to any modification treatment, the equiaxed phase of the ZnAl4-1 alloy that has been modified tends to have a more uniform distribution and is smaller after the treatment. The eutectic area expands, and the structure as a whole appears more uniform and well-balanced.
Under the influence of rare earths, many equiaxed phases and grain boundary corrosion-prone phases have gradually transformed into eutectoid phases. This undoubtedly creates conditions for improving the mechanical properties of alloys, reducing the amount of intergranular corrosion, and improving the aging resistance of the material. In addition, in order to gain a deeper comprehension of the distribution of the primary elements in the alloy after it has been modified, it has been reached the conclusion that the ZnAl4-1 alloy has been modified. Even in the cast state, the distribution of aluminum, copper, and elements that have been modified is relatively even, and there is no enrichment. It has been verified that the rare earth elements are dispersed uniformly throughout the modified ZnAl4-1 alloy.
2) Impact on the internal structure of parts produced by die casting
Whether in the primary phase or the eutectic phase, the structure of the ZnAl4-1 alloy die-casting after modification is more refined zinc alloy die casting supplier, diffuse, blunt, and uniform than that of the ZnA14-1 alloy without modification. This is true whether the structure is viewed in terms of the eutectic phase or the primary phase. The influence that rare earth elements have on the mechanical properties.
Shenzhen Yuge used the specimens specified in JB3072-82 to measure the mechanical properties of the alloy. Additionally, the die-casting process parameters of the specimens were controlled in the following range: die-casting temperature 420440°C, the mold temperature zinc alloy die casting supplier is 130150°C, the injection specific pressure is 4O50MPa, the filling speed is 1215m/s, and the holding time is 30 minutes. This was done so that the effects of rare earth modification treatmentThe modified ZnAl4-1 alloy has a b value of 298 MPa and a b value of 2. At the same time, in order to further confirm the reliability of the test, microcomputer statistics were used to sort out the test data obtained under different conditions for the unmodified ZnAl4-1 alloy and the modified ZnAl4-1 alloy. This was done in order to compare the results of the two types of ZnAl4-1 alloy.
In addition, the alloy solidification shrinkage was evaluated, and the findings demonstrated that the tensile strength and hardness of the ZnAl4-1 die-cast zinc alloy treated with rare earth modification increased by more than 10% in comparison to the ZnAl4-1 die-cast zinc alloy that did not include any modification. During the processing of the latter, there is less of a propensity for cracking and deformation, and there is an improvement in both the surface finish and the qualification rate. It is possible to significantly alter the metallographic structure characteristics of die-cast zinc alloy by adding 0.5% to 1% of rare earth. This can optimize the structure, refine the grains, remove impurities at the grain boundaries, and suppress the harmful effects of impurity elements. The former has a lower tendency for intergranular corrosion when compared to the ZnAl4-1 die-cast zinc alloy that has not been modified by rare earth modification. This is due to the fact that rare earth modification was not performed on the latter.