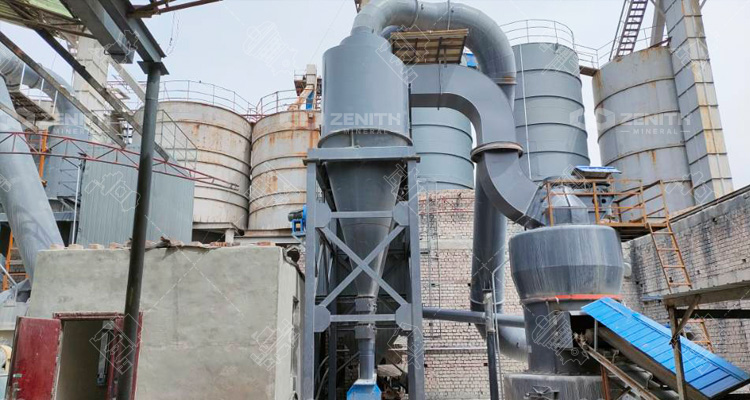
Grinding mills are essential equipment used across various industries to reduce solid materials to fine powder sizes. Effective mill operation relies on optimizing related processing parameters. However, maximizing efficiency also requires ensuring mills receive proper maintenance with scheduled downtime for repair and component replacement.
This article details critical tips and best practices to maintain Grinding Mill functionality for long-term, trouble-free operation. Regular inspection and servicing activities will be outlined to minimize unplanned outages. Methods for improving mill availability and performance through condition monitoring are also explored. The guidance provided aims to assist plant operators in establishing comprehensive grinding circuit maintenance programs.
1.Inspection Schedules
Setting predefined inspection schedules helps proactively identify potential issues before major breakdowns occur. The frequency varies by mill type and operating conditions but can include:
Daily - Check lubrication levels, operating parameters like vibration, noise and temperature. Inspect discharge conveyors.
Weekly - Grease moving parts, check bearing surfaces and structures for wear. Monitor dust collectors.
Monthly - Clean interior, replace damaged liners. Check gearboxes, motors and electricals.
Quarterly - Disassemble smaller parts, fully inspect major components. Conduct overhauls if needed.
Yearly - Remove mechanical equipment for detailed inspections and repairs during scheduled shutdowns. Replace large worn parts.
Condition monitoring using vibration, corrosion and thermography analyses can supplement inspections by continuously evaluating mill health. Abnormal readings warrant closer attention to prevent deterioration escalating.
2.Proper Lubrication
Maintaining appropriate lubrication of grinding mill is essential for bearings, gear reducers, drive shafts and other moving parts subjected to heavy loads or grinding slurry/dust exposure. Use industry-rated greases resistant to contaminants and temperature extremes encountered.
Follow manufacturers' lubrication schedules and grease specifications. Monitor consumption to detect over- or under-lubrication. Thoroughly purge and re-lubricate during maintenance periods, paying attention to sealed-for-life components requiring factory service. Neglecting lubrication needs leads to accelerated wear and fatigue damage over time.
3.Motor Care
Electric motors powering mills endure harsh conditions, warranting diligent maintenance. Clean enclosing fan covers regularly to ensure airflow isn't impeded. Check drive belts for tension, alignment and condition. Monitor temperatures, bearing noise and motor current draw against baselines to detect issues early.
Perform scheduled cleaning, inspection and testing as per supplier recommendations. Replace worn contacts, bearings and other worn parts promptly to avoid motor failures disrupting operations. Thermography surveys help identify weaknesses needing attention prior to breakdown events.
4.Structural Integrity
Regularly inspecting mill structures for cracks, loosening bolts or corrosion is a must. Visual checks allow detecting fatigue-induced flaws near welds and high-stress areas before failure. Non-destructive testing during detailed inspections supplements visual oversight.
Tightening structural mounting bolts to pre-set torques prevents vibrations from inducing failures over time. Proactively replace corroded bolts and any damaged structural elements found. Conduct welding repairs professionally as required to maintain structural integrity safely handling material loads and grinding forces.
5.Wear Parts Management
Maintaining proper wear parts inventory levels supports timely replacement when mill liners, discharge trunnions and ball/pebble charges show excessive wear during inspections. Ordering replacement stock allows scheduling change-outs during planned downtimes without production interruptions.
Monitor and track wear rates based on runtime hours and material properties to optimize part life. Sectioned discharge conveyors and high-wear trunnion zones allow partial replacement versus complete liner changes. Grinding media should likewise be checked and replenished according to manufacturer recommendations.
6.Repair Practices
Promptly address issues identified during inspections to prevent escalation requiring more extensive repairs. Ensure qualified technicians perform all mill work safely according to equipment manuals and industry best practices.
Maintain clean, organized work areas and use only OEM-approved parts for repairs. Conduct non-destructive testing as needed. Strictly follow lock-out/tag-out protocols when servicing energized equipment. Thoroughly clean and inspect systems before restarting to avoid defects causing secondary damage. Proper training reduces risks to personnel and assets.
7.Maximizing Uptime
Formulating strategic maintenance plans according to equipment and material specifics maximizes grinding mill availability sustaining process efficiency targets. Including condition monitoring and proactive replacement of worn components shortens repair downtime extending mill lifetimes significantly.
With consistent adherence to the guidelines provided, operators can realize grinding operations operating at designed throughput with minimized unscheduled outages keeping maintenance costs optimized over the long run.