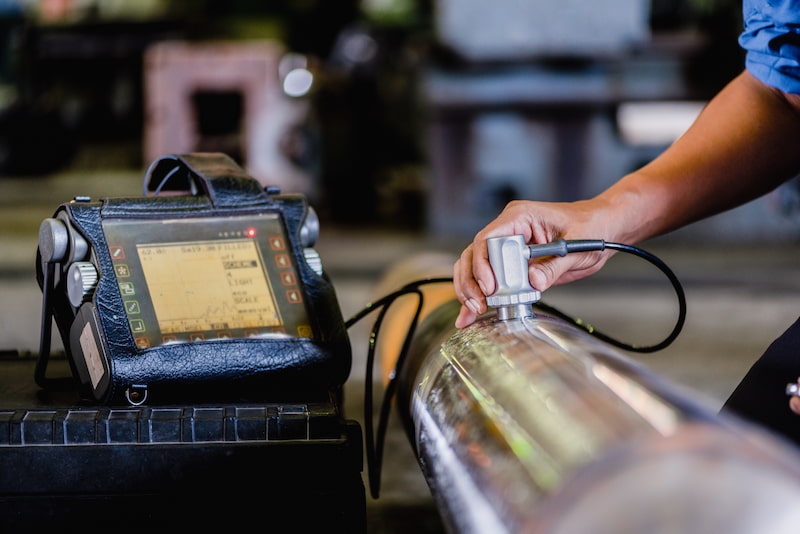
Non-destructive testing (NDT) refers to a wide range of analysis techniques used in science and industry to evaluate the properties of a material, component or system without causing damage. Within the field of NDT, ultrasonic testing is one of the most widely used and reliable methods for inspecting a material for internal flaws or discontinuities. With increasingly stringent quality standards across various industries, ultrasonic NDT equipment has become indispensable for ensuring product safety and reliability.
What is Ultrasonic Testing?
Ultrasonic testing, also known as ultrasonography, involves the use of high-frequency sound waves to examine materials. In this technique, high frequency sound waves in the range of 0.1 MHz to 15 MHz are introduced into a material using a transducer. As the waves encounter internal flaws, discontinuities or changes in material properties, they either reflect back to the transducer or get refracted. The reflected or refracted signals are then processed and analyzed to determine the location, orientation and size of any defects within the material.
Ultrasonic testing provides several advantages over other NDT methods. It can inspect thick materials and locate flaws within a wide range of applications. Moreover, it is highly portable and the instruments are relatively inexpensive compared to other techniques like radiography. The technique does not use any harmful radiation making it safe for operators. Thanks to these benefits, ultrasonic testing is widely used in industries like aerospace, power generation, oil & gas, construction and more.
Applications in Aerospace Industry
Ultrasonic testing plays a vital role in ensuring safety and integrity of aerospace components. It is commonly used during manufacturing to detect casting defects and check for lamination or porosity in composite materials. Finished parts like engine blades, landing gear components and structural joints also undergo 100% UT inspection. This helps manufacturers eliminate faulty parts and reduce risks of in-flight structural failures.
Ultrasonic Non-Destructive Testing Equipment is also extensively used for non-destructive evaluation of aircraft structures and engines during routine maintenance checks. Critical areas like wing and fuselage joints, engine casings and turbine blades require periodic testing to monitor fatigue damage accumulation over the lifetime of an aircraft. By accurately detecting cracks at an early stage, UT helps prevent catastrophic accidents and extends the service life of aircraft.
Oil & Gas Industry Applications
Process equipment in refineries and gas plants undergo stringent quality control checks since even small faults can lead to hazardous leaks. Components like heat exchangers, pressure vessels, pipes and storage tanks are ultrasonically tested for fabrication defects, corrosion damages and crack growth. Regular UT surveys determine the structural integrity of aging infrastructure and schedule repair/replacement on a priority basis.
Ultrasonic phased array technology is ideal for voluminous weld inspections on offshore oil rigs, pipelines and storage facilities. The technique allows rapid scanning of entire welds from one setup location. UT also plays a big role in validating the quality of critical pipeline girth welds to assure safety and prevent environmental risks. Non-destructive weld inspections according to international standards help operators minimize unplanned downtime and maximize asset life.
Power Generation Industry Usage
Ultrasonic testing finds extensive applications in the power industry to ensure safety and long term reliability of facilities. Critical components in fossil fuel, nuclear and hydroelectric stations undergo 100% UT inspection during manufacturing and pre-service testing to eliminate welding defects. Operating equipment like pressure vessels, steam turbines, generator components and piping undergo periodic testing to detect corrosion damage, crack initiation and growth over time.
Structural integrity assessments of reactor pressure vessels, containment buildings and pipelines transporting radioactive/toxic materials rely heavily on UT technology. The technique also helps monitor fatigue crack propagation in reactor components and determine residual lifetime assessment of aging facilities. Advanced ultrasonic phased array/TOFD systems have automated much of the inspection process, improving inspection coverage and productivity.
Construction Industry Adoption
Demand for high-rise buildings, bridges and other civil infrastructure has increased the importance of quality construction methods. Ultrasonic testing helps validate welding quality on rebar, structural beams and columns during fabrication to minimize in-service failures. Stress concentrations are also effectively monitored using UT to optimize designs and retrofit requirements.
Non-destructive methods have gained prominence with the structural health monitoring (SHM) of legacy structures. Periodic UT surveys help inspect for deteriorations in concrete and detect corrosion-induced damage in critical load bearing members well before visible signs appear. This allows condition-based maintenance decisions and rehabilitation measures, extending lifespans sustainably and safely.
Future Scope and Advancements
The non-destructive testing domain is rapidly evolving with technological progress. Advances like phased array UT, time-of-flight diffraction (TOFD) and guided wave testing have significantly enhanced inspection capabilities. Computer-aided UT systems are automating data capture and analysis for improved inspection quality and productivity. Integration with internet of things (IoT) will facilitate remote operational monitoring of assets globally.
New high-frequency sensors and advanced transducers will aid enhanced resolution of defects. The development of 3D volumetric ultrasonic techniques promises whole component scanning at a fraction of time compared to contact methods. Novel dual-modality techniques fusing UT with complementary methods like eddy currents, shearography or thermography augur wider defect detection capabilities. Overall, ultrasonic NDT will play a critical role in ensuring structural integrity, safety and reliability across various industries in the coming years.
Get More Insights on this Topic- https://www.newswirestats.com/ultrasonic-non-destructive-testing-equipment-is-one-of-the-most-widely-used-and-versatile-ndt-methods-for-inspecting-metallic-and-non-metallic-materials/