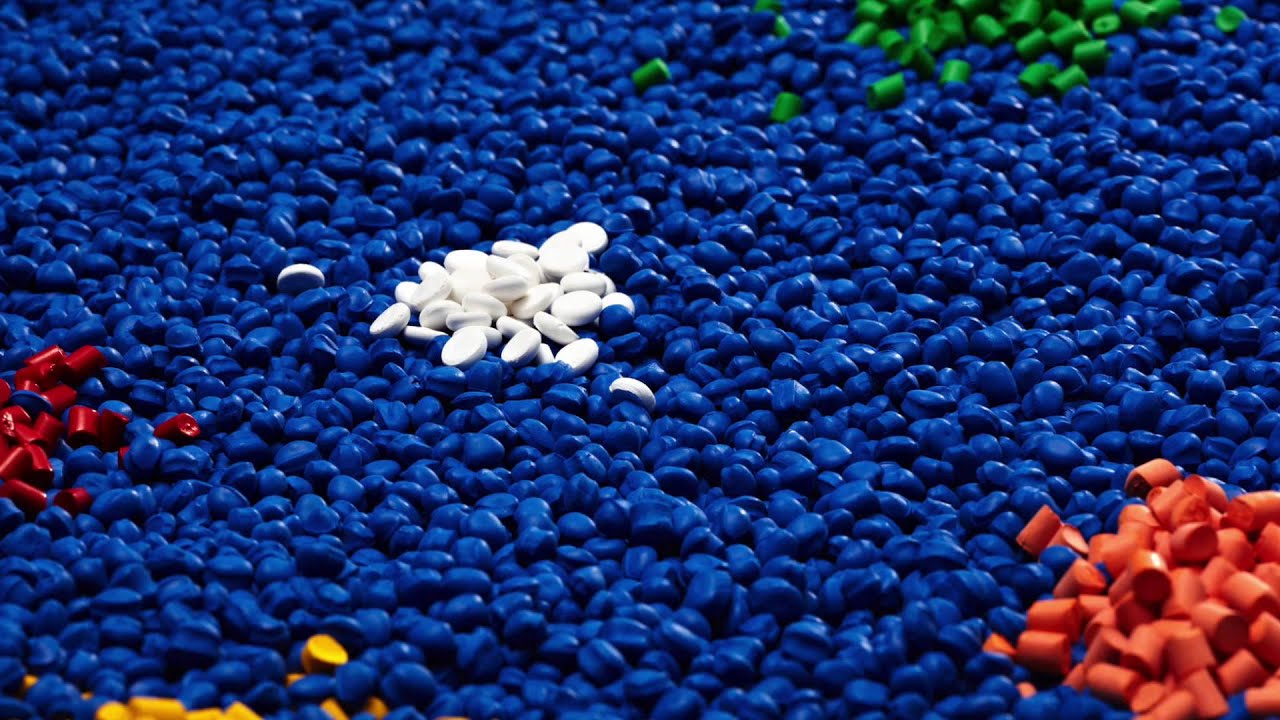
Thermoplastic elastomers (TPEs), also known as thermoplastic rubbers, are a class of copolymers or a physical mix of polymers that consist of materials with both thermoplastic and elastomeric properties. TPEs can be repeatedly softened and hardened by heating and cooling, respectively, and are different from conventional thermosetting elastomers such as vulcanized rubbers in that they do not undergo a chemical change which creates irreversible crosslinks when heated. This unique combination of properties allows TPEs to be easily processed and recycled like thermoplastics yet also have the functional performance of vulcanized rubbers.
History and Development
The development of thermoplastic elastomers can be traced back to the 1960s when new block copolymers were created that exhibited both thermoplastic and elastomeric behaviors. Some of the earliest and most widespread TPEs include styrenic block copolymers (SBCs) such as styrene-butadiene-styrene (SBS) and styrene-isoprene-styrene (SIS). These thermoplastic vulcanizates (TPVs) consisted of dispersed rubber particles crosslinked within a continuous thermoplastic phase. Since then, other classes of TPEs such as thermoplastic polyolefins (TPOs), copolyester elastomers, and thermoplastic polyurethanes (TPUs) have been invented and commercialized to expand the range of properties available. Constant research and innovation have allowed TPEs to replace traditional thermoset rubbers in many applications.
Properties and Characteristics
Some key attributes that distinguish thermoplastic elastomers from thermoset rubbers include:
- Melting behavior: TPEs soften and melt when heated above their melting/glass transition temperature but do not undergo vulcanization. They solidify upon cooling and can be reshaped repeatedly.
- Recyclability: The thermoplastic nature of TPEs allows simple recycling just like ordinary plastics by remelting and reforming. Vulcanized rubbers cannot be remolded.
- Processing versatility: TPEs can be processed using common thermoplastic techniques like injection molding, extrusion, blow molding etc. allowing precision shaping and automated production.
- Improved flexibility: Without vulcanization, TPEs demonstrate superior softness, flexibility and elongation properties compared to cured rubbers.
- Wide range of properties: Different TPE families including SBCs, TPUs and TPOs provide a variety of hardnesses, tensile strengths, temperatures stability and other performance traits.
Major Applications
Due to their advantageous characteristics, Thermoplastics Elastomers find widespread use in many application areas:
Automotive
- Hoses, gaskets, seals - TPE hoses are commonly used in radiator, brake and fuel applications. Their flexibility matches vulcanized rubber hoses.
- Interior - Seals, buttons, trim components utilize the soft-touch attributes of TPEs. TPUs are often used.
Electrical and Electronics
- Wire and Cable Insulation - Materials like TPUs provide needed insulation and jacketings.
- Connectors and Plugs - Housings, seals and other components call for TPE resilience and ease of processing.
Healthcare
- Medical Devices - TPEs enable minimally invasive devices with bellows, valves, seals from SBCs and TPUs.
- Orthopedic Products - Splints, supports, soft bracing use TPOs and thermoplastic polyamides.
Footwear
- Soles and Heels - TPE formulations deliver long-lasting cushioning and wear characteristics superior to PVC.
With their adaptability, these versatile engineered polymers continue gaining ground in traditional rubber goods domains and beyond. Advancing production techniques and newer TPE compositions further fuel novel applications on the horizon.
Future Prospects
As environmental and sustainability issues rise up the global agenda, thermoplastic elastomers are well-positioned to capitalize on their recycling-friendly nature compared to conventional non-recyclable rubbers. Regulatory tailwinds promoting greener materials coupled with strong ongoing R&D portend impressive future growth trajectories for TPE demand across diversifying markets. Automotive electrification, burgeoning healthcare sectors in Asia and the production migration toward lower-cost thermoplastic technologies particularly in China point to auspicious long-term industry drivers. Overall, the unique fusion of rubber-like performance with plastic-like processing in thermoplastic elastomers has undoubtedly cemented their prominence as indispensable specialty materials for the modern age. Continued technical progress promises to further broaden the boundaries of these highly flexible, resilient and recyclable thermoplastic polymers.
For More details on the topic:
https://www.newswirestats.com/thermoplastic-elastomers-size-and-share-analysis/