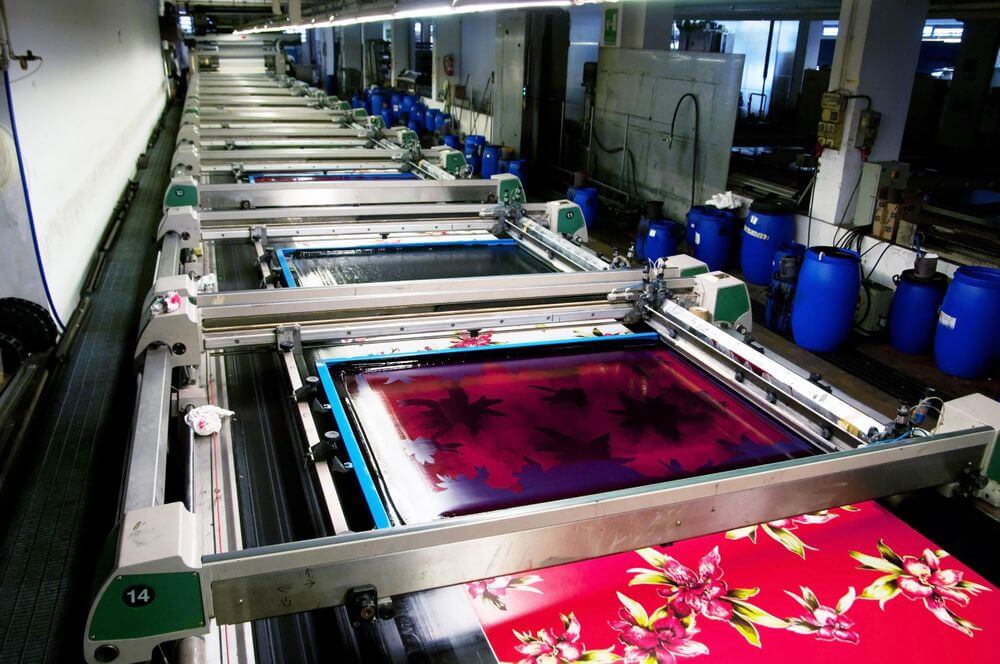
What is Screen Printing?
Screen printing is a printing technique where a mesh is used to transfer ink onto a substrate, except in areas made impermeable to the ink by a blocking stencil. A blade or squeegee is moved across the screen to fill the open mesh apertures with ink, and a reverse stroke then causes the screen to touch the substrate momentarily, enough for the image to transfer.
Screen printing is considered a low-cost process that requires relatively inexpensive equipment, allows printing onto uneven or complex surfaces, and provides durable, opaque printed images that are widely used in textiles, packaging, home decoration, and consumer goods like clothing and signage.
Evolution of Industrial Screen Printing
Screen printing started as a manual process but evolved with technological innovations like automated presses and digital design capabilities. Early manufacturing used carved wooden blocks or hand-cut stencils to apply paint or ink onto fabrics. In the 19th century, metal and plastic serigraph screens became commercially available, allowing for mass reproduction of posters and advertisements.
After World War II, screen printing advanced significantly with the development of photo-emulsion printing methods that let designers create stencils using high-contrast films and exposure units. This photosensitive process enabled complex multicolor images and made screen printing viable for industrial production. In the 1970s, computer-aided design software allowed digital artwork files to output photo stencils directly without films. Today, CAD/CAM systems fully automate stencil production for high-volume commercial printing.
Industrial Screen Printing Processes
Modern industrial screen printing relies on automation throughout the production workflow. Design files are created digitally and output as photopolymer emulsion stencils using high-resolution imagesetters. Automatic screen printing presses register and apply multiple ink colors quickly and accurately. Curing equipment then dries inks before finishing processes.
Key industrial screen printing steps include:
- Stencil Making: Digital art is output to photopolymer-coated screen meshes using UV light to cure open or blocked ink areas.
- Screen Mounting: Metal frames precisely hold tensioned meshes for printing. Registration pins ensure correct color alignment.
- Automatic Presses: Substrates are loaded onto conveyors synchronized with print station movements for multi-color overlay registration.
- Flash Curing: UV or infrared lamps quickly dry ink layers between color applications.
- Inspection and Finishing: Quality control checks print quality before products undergo die cutting, packaging, or other finishing operations.
- Cleaning and Reclaiming: Used screens are cleaned to remove ink buildup so emulsion can be reapplied and screens reused.
Strict process controls ensure high print quality and consistency at high production speeds required by industrial screen printers. Precise ink deposition, color overlay accuracy, and fast curing are essential.
Applications and Industries Using Screen Printing
A wide variety of industrial and commercial applications employ screen printing due to its capacity for high-volume production of durable, colorfast printed products at relatively low unit costs. Key screen printing applications and industries include:
- Textile Printing: Garments, home furnishings, signage, and other textile goods can utilize multicolor screen printing with rotary or flatbed printing.
- Packaging: Food, cosmetic, pharmaceutical, and other product packages get printed labels, graphics, or direct prints using screen inks approved for indirect food contact.
- signage and Display Graphics: Large format posters, banners, vehicle/building wraps, and point-of-purchase displays leverage the ability to print onto varied substrates like vinyl, paper, fabric, and corrugated.
- Electronics: Conductive inks screen print circuit boards, touch sensors, RFID antennas, and other electronic components onto rigid and flexible substrates.
- Ceramic Decoration: Underglaze inks on clay products like tiles and tableware are fired to produce vibrant, durable designs.
- Industrial Products: Machine parts, equipment labels, and other durables use screen printing for product identification and decoration.
No other printing process can match screen printing’s versatility across such a broad spectrum of commercial applications requiring mass-produced, weatherproof, and long-lasting printed graphics. Its economic advantages of low per-unit costs and ability to print onto diverse substrates continue driving growth in industrial screen printing.
The Future of Screen Printing Technology
While screen printing production workflows have become highly automated, continued technological innovations aim to improve press throughput, print precision, and broader application ranges. Advances in stencil imaging resolution allow more detailed images, and new emulsion chemistries increase stencil durability for longer print runs. Ultraviolet-curable inks and instant-dry formulations speed printing cycles.
Digital workflow integration offers tighter process control. Computerized color management enhances color accuracy between file creation and print output. In-line quality inspection with spectroscopic sensors identifies defects immediately to reduce waste. Advanced motion control enables multiaxis printheads to apply unique textures or variable ink deposits programmatically.
Newer applications utilize screen printing expertise in hybrid processes. Examples include printed electronics combining circuit printing with embedded component assembly and 3D object decoration augmenting molded parts with layered surface graphics for industrial equipment. Combining screen printing's strengths with complementary technologies sustains its essential role in diverse modern manufacturing.
From its origins as a manual art, screen printing has steadily industrialized through manufacturing process mechanization and digital workflow integration. Today's highly automated screen printing production meets demanding requirements across diverse application areas by offering economical mass production of durable, vibrant graphics onto various substrates. Continued technology evolutions ensure screen printing remains a foundational industrial printing process well into the future by enabling new capabilities for product identification, decoration, and functional printing.
Get more insights on this topic: https://www.ukwebwire.com/screen-printing-is-a-printing-technique-where-a-mesh-is-used-to-transfer-ink/