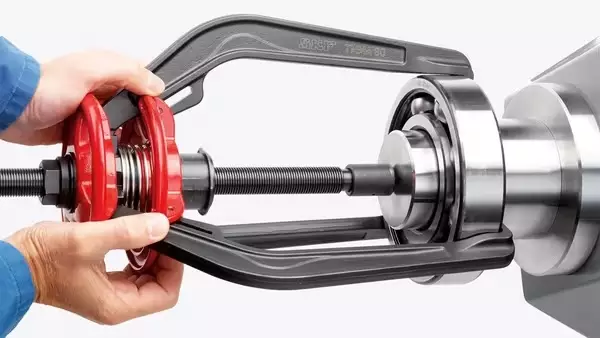
Every bearing will sooner or later become unserviceable over its intended life. Even when it is installed and serviced according to manufacturers recommendations. Raceway surfaces and rolling contact surfaces are subjected to compressive loads, and the surfaces eventually become subject to flaking.
However other failure modes which are a more common cause of failure include seizing, breakage, wear, false brinelling, and corrosion. In many cases, these failures are due to improper handling, poor selection, bad bearing design and poor maintenance. This article is intended to provide an overview discussion on key points to follow as a standard maintenance guideline.
Inspection of Bearings
Inspecting the bearings after initial installation while the machine is in operation will help in preventing future bearing failures. The following is a list of procedures you should follow.
Inspection when machine is running
Check the bearing temperatures and bearing vibration/noise and determine if the bearing is lubricated properly or needs more lubrication.
Inspection of bearings after operation
Bearings should be carefully examined in periodic maintenance inspections for you to note any damage. If damaged the bearing can be analyzed and the cause of failure determined. Remedies can then be provided to prevent further problems.
It is important to determine inspection procedures and establish regular inspection intervals.
Bearing Temperature
Bearing temperature generally will increase at start-up and stabilize at a temperature slightly lower than at start-up (normally 10 to 40 ̊C higher than room temperature) over a set period of time. The time for the operating temperature to stabilize depends on the size, type, speed, and lubrication. The heat dissipation depends on the operating environment of the surrounding components. The stabilization can range from as little as 20 minutes to several hours.
The thing to watch is if the bearing temperature does not stabilize but continues to rise. If the temperature continues to rise it may be the result of one of the following reasons:
- Extremely insufficient or excessive lubricant
- Poor installation of the bearings
- Extremely small bearing clearance or extremely heavy load
- Extremely high friction between lip and seal groove
- Improper lubricant type
- Creep between the fitting surfaces
If any of these conditions are present then operation should be stopped and an appropriate corrective action should be taken. A desirable bearing operating temperature is generally below 100 ̊C.
Mounting and Dismounting of Bearings
For bearing handling use gloves. When moving larger bearings use special lift and carrying tools designed specifically for mounting and dismounting bearings. Both SKF and Schaeffler offer these special types of tools and can be purchased from PIB by going to www.pibsales.com. The use of heat and oil-resistant gloves is recommended when handling hot or oily bearings. These gloves should have a durable outside and a soft non-allergenic inside. We recommend SKF TMBA gloves.
If large, heavy bearings are to be moved or held in position using a lifting tackle they should not be suspended at a single point utilizing a steel band or fabric belt. A spring between the hook of the lifting tackle and the belt facilitates proper positioning for the bearing when it is to be pushed onto a shaft.
Alignment tools
Misalignment of shafts, belt drives, and chain drives will contribute to machinery breakdowns.
Accurate alignment will prevent a large number of machinery breakdowns and reduce the number of shutdowns. Accurate alignment will help to extend the life of the bearings and machines.
In today’s challenging environment for cost reduction, the necessity of accurate alignment is needed more than ever.
Preparing for Mounting of bearings
Prior to the mounting process, one must ensure that the bearing, the shaft, and the housing are clean and free of any foreign particulates. It’s important to remember that even microscopic debris, when lodged between rolling elements, will cause excessive wear. Bearings should be kept in their original packaging until the moment of installation to prevent contamination.
Maintenance Tools
1. Bearing Pullers
A bearing puller is a mechanical tool specifically designed for the dismounting of bearings from a shaft. It typically consists of a central mandrel and two or more adjustable arms that grip the bearing securely. By turning the mandrel, a constant axial force is applied, enabling the removal of the bearing without damaging adjacent components. Different configurations, such as three-arm or two-arm pullers, cater to various bearing sizes and applications.
2. Bearing Induction Heaters
These devices utilize electromagnetic induction to generate controlled heat, facilitating the thermal expansion of bearings. Comprising a coil encased within a metallic core, bearing induction heaters pass an alternating current through the coil, inducing a magnetic field. The bearing, when placed within this field, heats uniformly. This controlled heating ensures that the bearing can be mounted onto the shaft with reduced force, minimizing the risk of installation damage.
3. Shaft Alignment Tools
Shaft misalignment can lead to uneven load distribution in bearings, reducing their operational life. Laser shaft alignment tools are designed to achieve precise alignment between two connected shafts. Utilizing laser diodes and detectors, these tools measure angular and radial deviations, providing real-time feedback to technicians. With such data, necessary adjustments can be made, ensuring optimal bearing function.
4. Lubrication Dispensers
Correct lubrication is vital for bearing longevity. Lubrication dispensers, which include manual grease guns and automatic lubricators, deliver a specified amount of lubricant to the bearing. Precision in lubrication application reduces frictional wear, prevents contamination ingress, and ensures efficient heat dissipation.
5. Stethoscopes and Vibration Analyzers
For diagnostic purposes, mechanical stethoscopes and vibration analyzers are employed. Mechanical stethoscopes, equipped with a probe, allow technicians to listen to the operational sounds of a bearing, identifying irregularities like pitting or misalignment. Vibration analyzers, on the other hand, measure the amplitude and frequency of vibrations from the bearing. By analyzing this data, one can ascertain issues like imbalance, misalignment, or early signs of wear.
Conclusion
Bearings play a pivotal role in machinery operation. Adopting a good maintenance strategy, as detailed in this discussion, can optimize equipment efficiency, minimize operational interruptions, and yield considerable economic benefits.
Still have questions or want to discuss something? Please Contact us at [email protected].