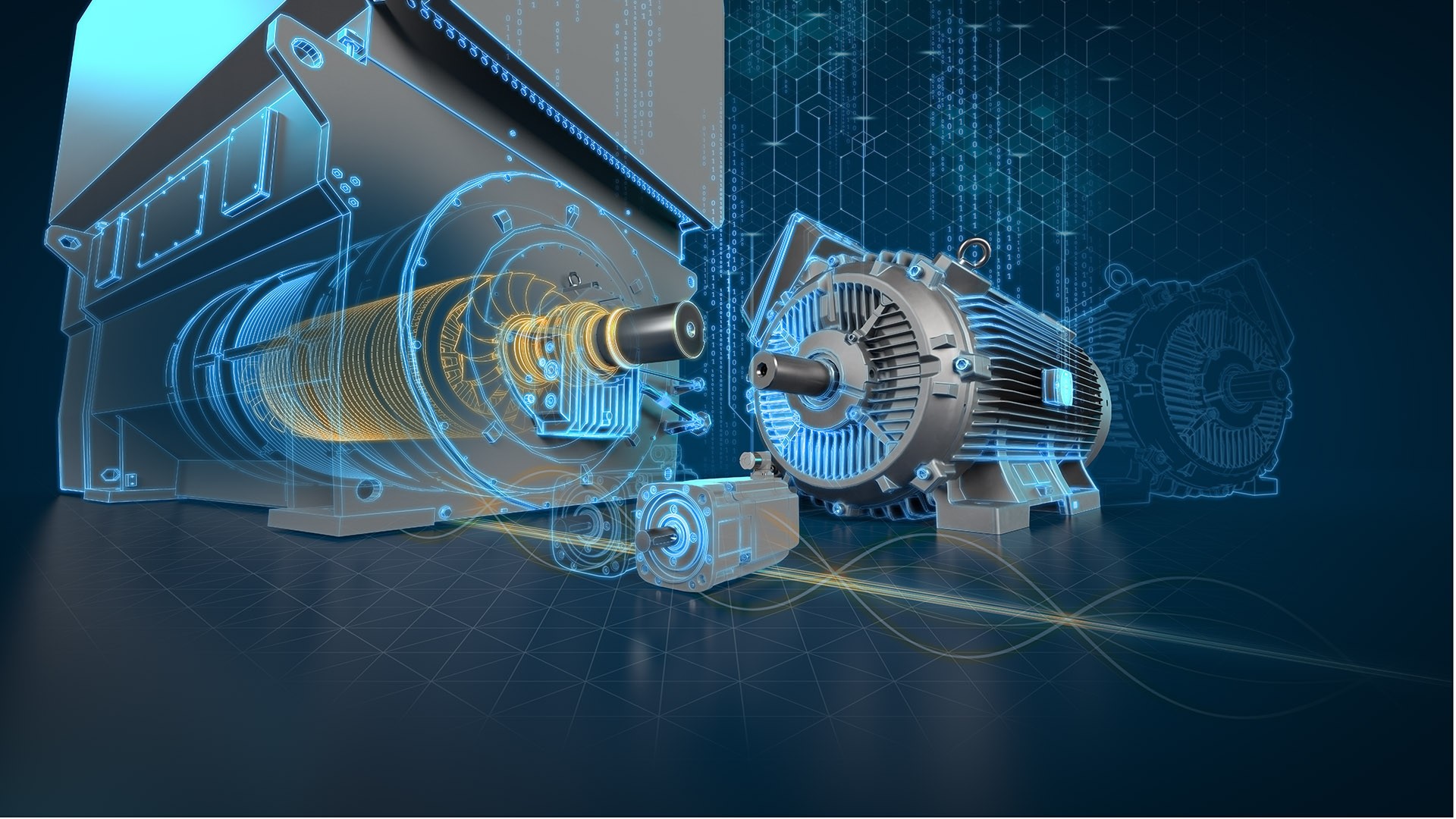
Motors are one of the most ubiquitous and important machines used across industries globally. Powering tools, equipment and entire manufacturing processes, industrial motors form the backbone of production facilities and fulfil a critical function. In this article, we will examine the types of motors commonly used in industrial settings along with their key features and applications.
Types of Industrial Motors
There are various motor types optimized for different industrial applications based on factors like workload, speed requirements, environmental conditions etc. Some of the major motor categories include:
AC Motors
Alternating current (AC) motors are the most widely used industrial motors due to their reliability, robustness and easy maintenance. The main AC motor variants are:
- Induction Motors: These are very durable and low maintenance. Ideal for constant workload applications like conveyor belts, machine tools etc. Different designs cater to low/high voltage and torque needs.
- Synchronous Motors: Offer high torque and power density. Used for heavy-duty tasks like steel rolling mills. Require precise speed regulation through electronic drives.
- Brushless DC Motors: Combine benefits of AC and DC motors. Commonly found in robotic arms, CNC machines due to compact size and ability to handle variable speeds.
DC Motors
Direct current (DC) motors function using direct flow of current and are suitable for applications requiring variable or precise speed control. Common types are:
- Brushed DC Motors: Inexpensive and easy to control but require brushes that sparks and wears out. Used in forklifts, drill machines etc.
- Brushless DC Motors: As discussed above, brushless type has replaced brushed DC motors in industrial automation due to increased reliability.
Specialty Motors
There are specialized motor designs for certain industry verticals or environmental extremes:
- Explosion Proof Motors: Used in hazardous/flammable areas with a thick coating and sealed enclosure for safety.
- High Temperature Motors: Insulated windings allow operation at over 200°C. Suitable for oil, gas, iron and steel industries.
- Waterproof Motors: Completely sealed to prevent water/moisture ingress. Ideal for marine, food processing, water treatment plants.
Applications of Industrial Motors
Having looked at the main motor types, let us explore some key industrial applications where they are commonly employed:
Material Handling
Motors power conveyor belts, lifts, cranes and other machinery for transporting raw materials and finished goods within factories and warehouses. AC Industrial Motors are a staple due to reliability under continuous use.
Production Machinery
Machine tools like lathes, mills, grinders incorporate DC or AC servo motors paired with drives to precisely control speed and motion. This enables automation of repetitive manufacturing tasks.
Packaging Lines
From filling to labeling to boxing, modern packaging is dominated by motor-driven equipment. DC motors enable flexible control of intermittent processes while AC variants run continuous belt production lines.
Heating, Ventilation and Cooling
Motors power fans, blowers, air compressors and pumps for HVAC systems that maintain optimal factory environmental conditions. Explosion proof and high temperature motors are crucial in some industries.
Factory Utilities
Motors power generators, pumps that supply power, water and compressed air utilities throughout industrial complexes. Submersible, waterproof variants handle outdoor liquid distribution.
Ongoing Advancements
Continuous innovation is enhancing motor efficiency, reliability, controllability and integration with digital technologies:
- New motor designs maximize energy efficiency to reduce operational costs and carbon footprint.
- Condition monitoring and IoT enable predictive maintenance to minimize downtime.
- Brushless and servo motor miniaturization allows more compact machinery designs.
- Advanced motor drives realize precise variable speed control for process optimization.
With factories increasingly relying on automation to boost output and quality, industrial motors will remain indispensable workhorses facilitating modern-day mass production. New applications are also emerging with technologies like 3D printing, robotics and smart manufacturing revolutionizing industries. Motors exemplify mechanization’s central role in global economic development.
Get more insights, On Industrial Motors