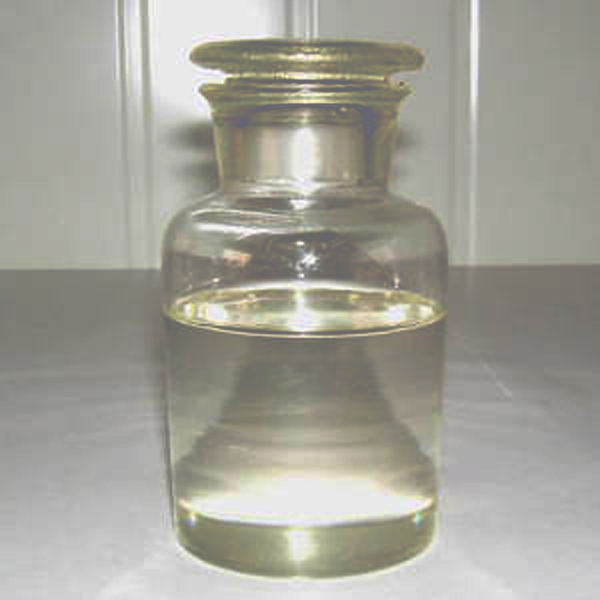
Chemical Structure and Properties
Vinyl acetate monomer (VAM) is an important organic compound utilized in numerous industrial applications. On a molecular level, VAM consists of an acetate group bound to an ethylene group. The chemical formula is CH3COOCH=CH2, consisting of a vinyl group bonded to an acetate ester. As an unsaturated monomer, VAM is capable of undergoing addition polymerization reactions to form polymers with varying properties depending on polymer structure and composition.
Some key physical properties of VAM include being a colorless liquid with a characteristic sweet odor detectable at low concentrations. The molecule is miscible in many organic solvents such as alcohols and ketones but is only partially soluble in water. VAM has a boiling point of 72°C and melting point of -99°C, allowing for versatility in processing and application methods. Safety is an important consideration as well, as VAM is flammable with a flash point of 10°C. Proper handling and storage precautions should always be followed.
Polymerization into Polyvinyl Acetate
Among its widespread commercial uses, Vinyl Acetate Monomer serves as the monomer building block for producing the polymer polyvinyl acetate (PVAc). Through radical vinyl polymerization, VAM molecules link together into long chains with the vinyl groups combining and acetate functional groups remaining intact along the backbone. The most common initiators are organic peroxides which generate free radicals to initiate chain reactions. This addition polymerization is exothermic and emulsion, solution, and suspension methods allow control over molecular weight, distribution, and product form.
The PVAc polymer product offers several defining traits. It is a thermoplastic possessing good film-forming abilities with viscosity decreasing as temperature increases. PVAc exhibits adhesive properties and has good tensile strength and flexibility even at low temperatures. While sparingly soluble in water, it dissolves readily in many common solvents such as alcohols, esters, ketones and glues. These traits make PVAc advantageous for use in numerous applications requiring adhesives, binders, coatings and more.
Adhesives and Wood Applications
Perhaps the largest commercial application area for VAM-derived PVAc polymers is in adhesives. PVAc works well as an adhesive resin due to its ability to form strong bonds with a variety of substrates like wood, paper, cardboard, metals and ceramics. Capable of forming both hot melt and cold-set adhesives, PVAc excels in woodworking and construction applications. Hot melt PVAc adhesives find extensive use in furniture assembly, shoe manufacturing, bookbinding and package sealing. Cold-set glues based on PVAc emulsions are utilized for wood lamination, nonwoven products and more.
Working directly with wood materials, dispersed PVAc emulsions are commonly employed as a key ingredient in woodworking primer paints, stains, and varnishes where they provide adhesion along with enhancing product viscosity and film formation. In addition, PVAc emulsions act as binders in the manufacture of wood-fiber board products like particleboard and medium-density fiberboard. The ability of PVAc to readily bond wood fibers helps create strong, uniform building panels for furniture, flooring and other construction applications.
Films, Coatings and Emulsions
PVAc also enables many other product forms beyond adhesives, taking advantage of its film-forming properties. PVAc resins are incorporated into vinyl PVC plastisols for coatings applied to fabrics, wallcoverings, and other materials requiring washability and flexibility. Vinyl-acrylic latex emulsions containing PVAc serve as paints and primers providing both adhesion and durability. Commonly used for architectural coatings on walls, ceilings, and trim, these water-based finishes have gained popularity as more eco-friendly alternatives. In addition, PVAc homopolymer and copolymer resins process into transit films like packaging wraps, book jackets, and blister packaging films where barrier properties and printability are important characteristics.
Modification and Crosslinking
While PVAc possesses many advantageous traits on its own, its performance can be further expanded upon through chemical modification of the VAM monomers prior to polymerization or crosslinking reactions post-polymerization. For example, copolymerizing VAM with other polar monomers like vinyl chloride, acrylic acid, or methacrylic acid introduces new functionality that impacts properties such as water resistance, adhesion, or permeability. Butyl acrylate is frequently copolymerized with VAM to produce latexes used in thick film coatings requiring flexibility and waterproofing. Crosslinking PVAc resins by reaction with carboxylic acids, amines, epoxies or isocyanates enhances dimensional stability, solvent resistance, and mechanical strength for demanding applications such as coatings for metal substrates. These tailored polymer derivatives expand the utility of VAM well beyond commodity uses.
Explore Our More Blogs on Vinyl Acetate Monomer