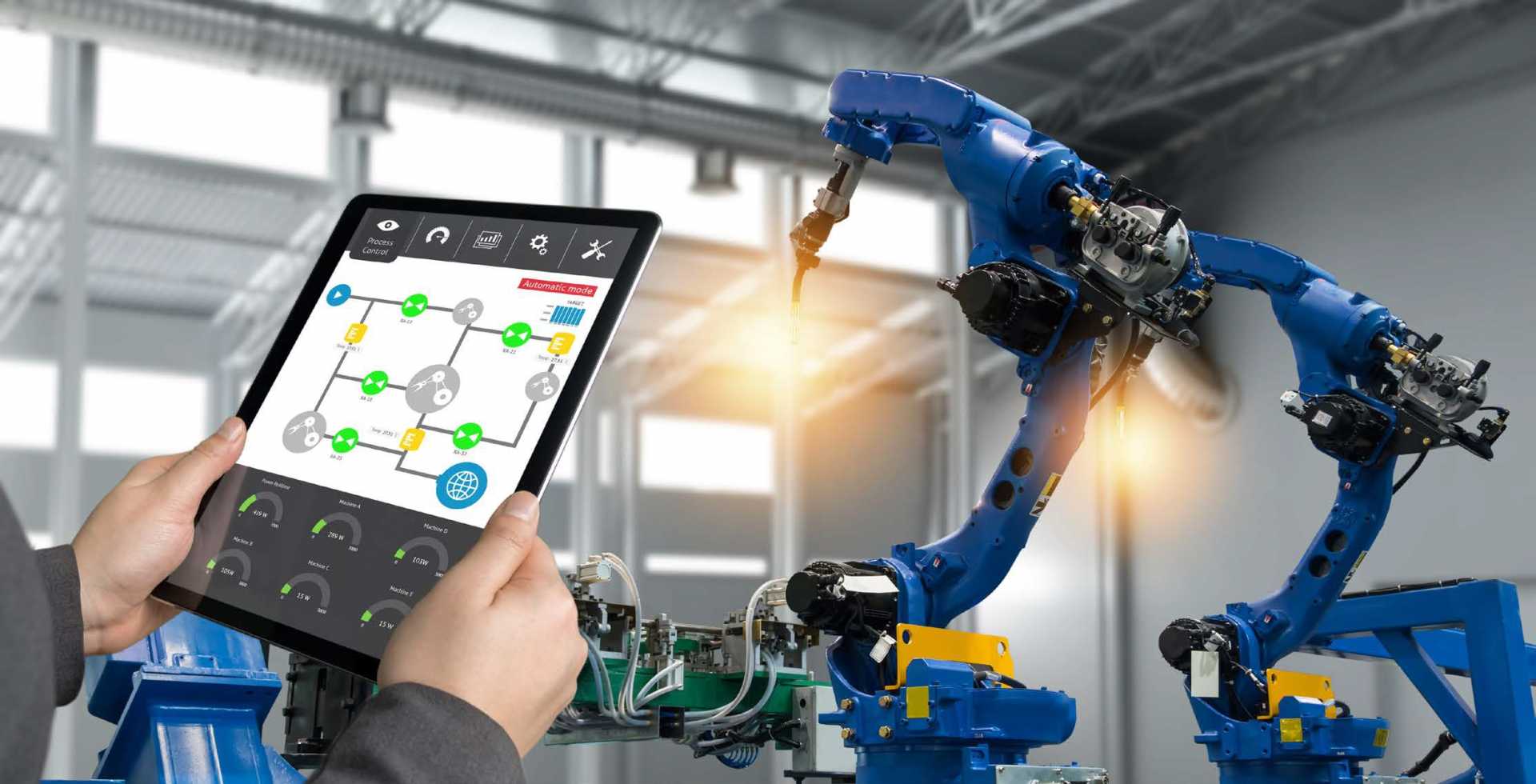
The manufacturing industry has witnessed tremendous changes in the past few decades with the rise of industrial automation and advanced technologies. One such major trend that is significantly impacting manufacturing processes and operations is the Internet of Things (IoT). IoT refers to the interconnection of physical devices, vehicles, machines and other items embedded with sensors, software, and network connectivity which enables these objects to collect and exchange data. The convergence of advanced technologies such as cloud computing, analytics, machine learning etc. with IoT is enabling manufacturers to tap into new business opportunities, achieve greater operational efficiency and optimize production processes.
Massive IoT Deployments in Factories
Manufacturers across sectors are recognizing the benefits of IoT and investing significantly in deploying IoT solutions at their production floors and warehouses. A survey by McKinsey found that over 70% of manufacturers have more than 1000 internet-connected machines and assets. Major IoT deployments include connecting industrial machines, quality inspection devices, AGVs, robots, sensors for monitoring temperature, pressure, vibrations etc. All these devices are generating huge volumes of real-time data which was previously difficult to access and analyze. IoT is enabling manufacturers to improve visibility across their entire value chain from raw material handling to finished product dispatch.
Predictive Maintenance and Reduced Downtime
Iot In Manufacturing enables predictive maintenance of industrial assets through continuous equipment condition monitoring. Vibration, temperature and motion sensors generate real-time data which is analyzed through machine learning algorithms to detect potential faults even before they occur. Predictive analytics helps identify maintenance needs in advance, schedule repairs and reduce unexpected downtime. This leads to improved asset reliability and availability. Avoiding unplanned outages helps maximize production uptime. For example, a semiconductor manufacturer leveraged IoT to predict failures in vacuum pumps and reduced downtime by over 30%. IoT based prognostic maintenance is revolutionizing after sales support and reducing maintenance costs.
Data-Driven Process Optimization
Manufacturers are leveraging data from connected machines, quality devices and operational systems to optimize manufacturing processes. IoT platforms aggregate real-time streaming data which is then analyzed to gain insights for driving improvements. Advanced analytics is helping extract meaningful correlations between process parameters like temperature, pressure, cycle times etc. and product quality. Manufacturers are able to detect defects and reroute defective products faster. Real-time monitoring and analysis further helps identify bottlenecks, rebalance workloads and improve changeover management to enhance overall equipment effectiveness. Data driven process optimization is enabling manufacturers to produce higher quality products with improved yields.
Supply Chain Visibility and Efficiency
IoT is enhancing supply chain visibility by connecting assets across the value chain. Real-time tracking of shipments, inventory levels, equipment condition etc. is helping manufacturers eliminate stockouts and manage just-in-time processes better. IoT solutions are improving demand forecasting accuracy by linking point of sales data with inventory levels. Blockchain integration is optimizing procurement processes and enabling traceability of raw materials. Suppliers can also monitor customer orders and collaborate better. IoT and analytics fuel efficient warehouse management through techniques like barcode scanning, RFID, automated guided vehicles and robots. This significantly cuts down operational costs, fulfillment time and improves customer satisfaction.
Smarter Manufacturing with Cloud and Analytics
Cloud platforms are playing a key role in manufacturing IoT deployments by providing scalable and flexible infrastructure to store, process and analyze massive volumes of data. Cloud-based Manufacturing Execution Systems (MES) are helping smaller manufacturers benefit from smart factory capabilities at lower costs. Analytics advancements like machine learning, neural networks and deep learning are enabling smarter applications. For example, computer vision coupled with AI is deployed for visual inspection and quality control. IoT sensors and infrastructure combined with cloud and advanced analytics are enabling the vision of a self-optimizing smart factory with automated processes, minimal human intervention and real-time decision making. This brings manufacturers closer to Industry 4.0 goals of flexibility, customization and operational excellence.
Wider IoT adoption is undeniably transforming manufacturing into an "Intelligent Enterprise". IoT combined with disruptive technologies helps gain entirely new insights. It connects people, processes and products across boundaries like never before. Manufacturers are realizing immense value through applications of IoT, cloud computing and analytics in enhancing productivity, process efficiency, reducing operational expenditures and enabling new revenue streams. Overall, IoT offers unlimited possibilities for innovation and reimagining future manufacturing.
Get more insights on Iot In Manufacturing
Also read related article on Kidney Cancer Drugs Market