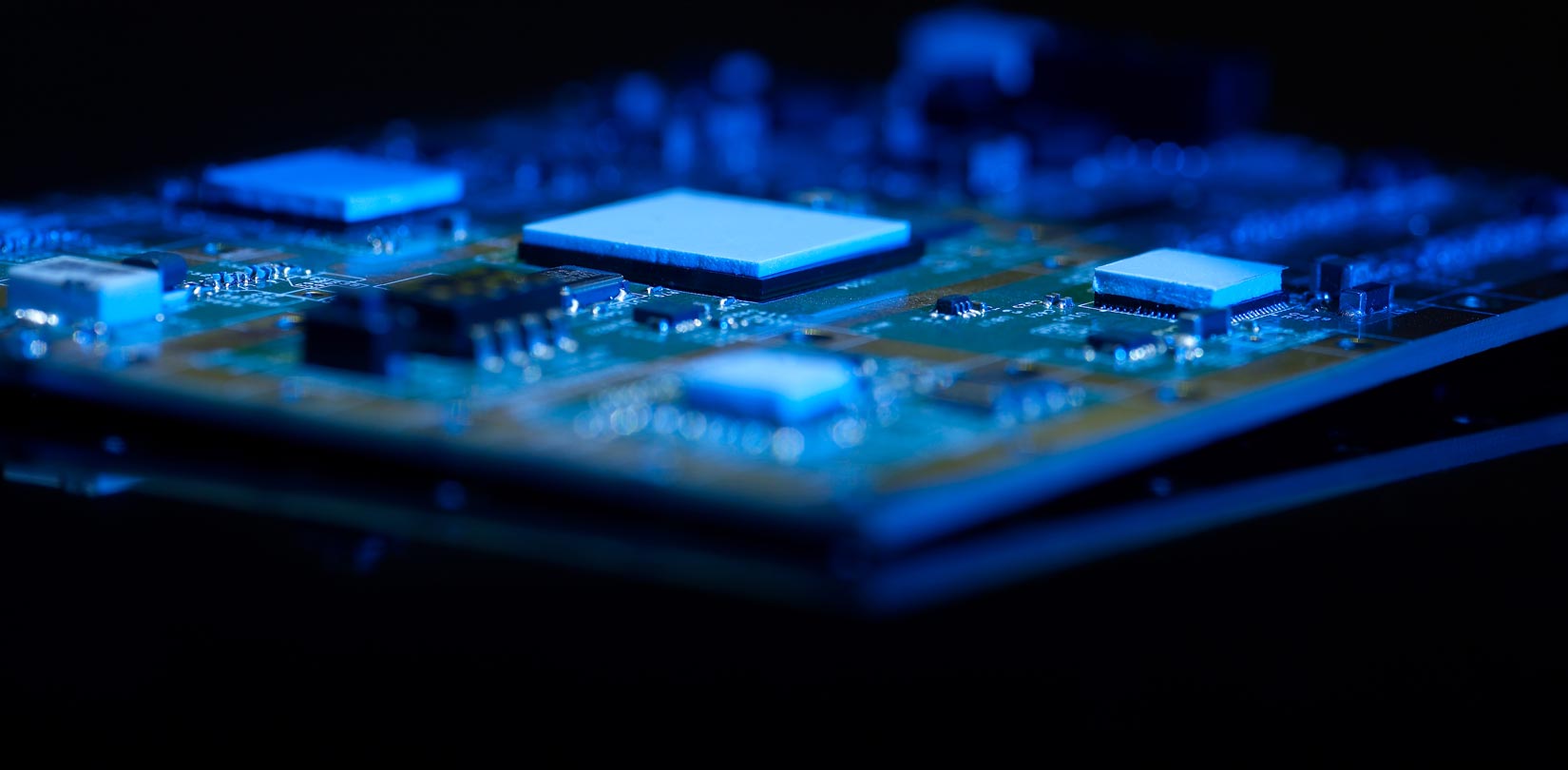
The continuous evolution and miniaturization of electronic devices has pushed the limits of heat dissipation and thermal management. As component density increases and sizes decrease, excess heat generated during operation poses serious risks if not transported out efficiently. This is where thermal interface materials play a vital role by facilitating heat transfer between components.
What are Thermal Interface Materials?
Thermal interface materials (TIMs) refer to any material designed to fill air gaps and promote thermal conduction between two solid surfaces. They provide a thermally conductive path to draw heat away from heat generating sources like processors, graphics cards, and power delivery components to heat sinks and heat exchangers. Without a proper TIM, the air gaps act as an insulator reducing heat transfer drastically. Common TIMs include greases, gap pads, phase change materials, and thermally conductive adhesives.
Importance of Thermal Interface Materials
The importance of TIMs cannot be overstated in electronics thermal management. As device wattage increases with each new generation, efficient heat dissipation away from hot spots becomes critical. Excessive temperatures can severely impact performance, reliability and lifespan of components. Some key impacts of inadequate thermal interface include:
- Increased junction temperatures lead to thermal throttling where processors downclock speeds to maintain safe operating temperatures. This degrades performance.
- Hot spots cause uneven heating which can lead to warping of components out of alignment over time due to differences in coefficient of thermal expansion.
- Excessive temperatures accelerate aging and breakdown of solder joints and interconnects. This negatively impacts reliability and reduces usable lifetime.
- In extreme cases, overheating can cause permanent damage to circuitry from heat related failures if thermal shutdown thresholds are exceeded.
By filling microscopic air gaps, TIMs reduce thermal resistance enabling more heat to flow out to external cooling solutions. This keeps critical components within safe thermal design windows allowing them to run at optimal speeds.
Common Thermal Interface Materials
Greases: Thermally conductive greases are the most widely used TIMs. They have a paste-like consistency and high viscosity which enables them to fill uneven surfaces and air gaps easily. Greases also handle component flexing and component replacement well. However, they tend to migrate or dry out over time reducing performance.
Gap Pads: Thermally conductive gap filling pads are solid and phase change from rubbery to rigid as they are compressed during installation. They maintain a thin bonded interface but cannot self-heal if interface is compromised. Gap pads offer durability but may leave small voids compared to greases.
Adhesives: Thermally conductive adhesives form strong metallurgical bonds between surfaces. They offer durability and prevent shifting over multiple thermal cycles. However, application can be messy and they cannot be reworked easily if removed. Adhesives require very clean, flat mating surfaces for optimal contact.
Phase Change Materials: PCM TIMs undergo reversible phase transitions from solid to liquid at certain temperatures to improve heat conduction. They maintain low resistance even during component flexing but have limited temperature operating range before melting point is reached. Selection of right PCM for application is important.
Applications of Thermal Interface Materials
With different properties, various TIMs fulfill requirements in different applications:
- CPUs and GPUs: Greases are most common as they can fill rugged surfaces and handle stresses of clamping without sacrificing performance long-term.
- Power Delivery Components: Gap pads provide thin, uniform bonds suited for power modules and MOSFETs handling frequent power cycling stresses.
- LEDs and Laser Diodes: Thermally conductive adhesives form stronger bonds suited for fragile optoelectronic packages requiring durability through thermal shocks.
- ICs: Thin, low resistance greases or gap pads minimize thermal impedance for high power density ICs without adding thermal mass.
- Avionics and Harsh Environments: Silicone based gap pads maintain flexibility through wide temperatures ranges encountered in avionics and automotive.
- Server Racks: High performance thermal phase change materials maintain integrity of tight gaps in crowded server racks.
Future of Thermal Interface Materials
The rapid pace of technology advancement brings new challenges for thermal interface materials as well. Nanoparticle filled greases with thinner bonded interfaces <10um are being developed to minimize resistance. Conductive adhesives utilizing graphene and CNT fillers push the boundaries of thermal conductivity. Liquid metal TIMs like gallium and indium alloys offer unprecedented performance but require special considerations for compatibility.
As device densities increase with adoption of 3D packaging and multi-chip designs, anisotropic interface materials able to conduct preferentially in desired directions will become important. Development of self-healing, electrically insulating TIMs able to autonomously repair interface damage also shows promise. With continual innovation, thermal interface materials will remain a crucial part of solutions ensuring electronics performance, reliability and longevity in the years to come.
Thermal interface materials play a vital role in heat dissipation from modern high-power electronics. By filling microscopic gaps, they facilitate thermal conduction to external cooling solutions. With different types available, selecting the right TIM suitable for the surface topology, stresses involved and thermal requirements is important. Ongoing research brings new materials to address future challenges. Proper selection and application of thermal interface materials thus remains a cornerstone of effective thermal management strategies.
Get more insights on this topic: Thermal Interface Materials