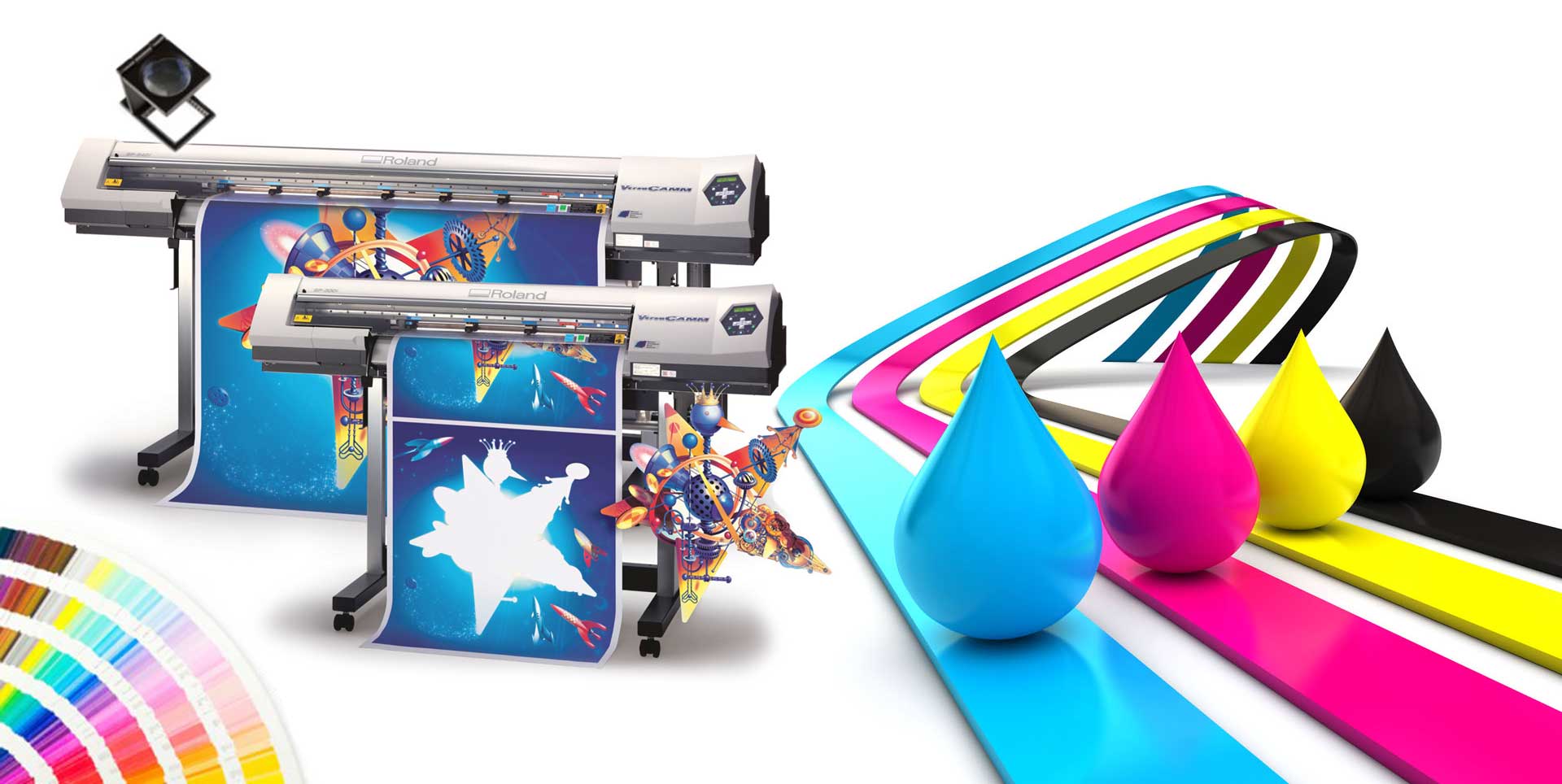
The Rise of Digital Printing
Digital printing has seen tremendous growth over the past decade. Where traditional printing methods like offset lithography dominated for most of the 20th century, digital printing is now becoming the norm. Some key factors that have driven this transformation include:
Lower upfront costs - Digital Printing have become much more affordable in recent years. This has allowed many small businesses and individual users to get into printing and design work without large capital investments. Lower costs have opened up many new applications and use cases for printing.
On-demand capabilities - Unlike traditional printing that requires large print runs, digital printing allows on-demand printing of variable content. This flexibility has expanded into new applications like personalized direct mail, short-run book publishing, and print-on-demand merchandising. Businesses no longer have to order more stock than needed.
Improved image quality - Early digital printers suffered from low resolution and inconsistent colors. However, advances in imaging technology have greatly improved the quality of modern digital presses. Many can now match or exceed offset printing in terms of resolution, color accuracy, and dimensionality. High-quality variable data and graphics are now possible.
New applications emerge as quality improves
Digital printing is now disrupting several large industries as capabilities continue expanding. Short-run packaging printing, textile printing, and mass customization are all areas seeing significant change driven by new digital applications.
Packaging goes digital
Traditionally, packaging printing required long runs due to high plate costs for offset lithography. This limited packaging design changes and customized short runs. Now digital presses are revolutionizing packaging by enabling on-demand customization at low minimums. This opens opportunities like localized product branding, personalized QR codes, and seasonal/promotional variations without excess inventory. Major brand owners are increasingly adopting digital packaging capabilities.
Textiles get personalized
The textile industry relies heavily on large-format digital printing as a greener and more customizable alternative to traditional screen printing. Garment printers have shrunk in size while expanding in quality and speed. This gives rise to on-demand custom apparel printing and mass personalized products. Consumers can now customize t-shirts, uniforms, and other textile goods in small quantities for events and fan merchandise.
Mass customization takes off
As personalization technologies improve, new opportunities emerge for mass customization across diverse industries. Footwear companies offer millions of color and design combinations produced digitally. Eyeglass manufacturers customize frames, lenses, and coatings for individual prescriptions. Other prospects include highly customized direct 3D printed products, and personalized large-format prints. Consumers have more control over product design and firms deepen engagement through customization at scale.
Challenges Remain for Wider Adoption
Substrates
While capable of handling most paper and synthetic substrates, digital printing still faces limitations with some traditionally printed mediums like packaging board, corrugated, and other heavy materials. Continuous innovation in printing technologies and newer materials is helping expand the range of substrates that can be printed digitally.
Color Gamut and Uniformity
Though quality has improved tremendously, digital presses still have a harder time matching the vivid and consistent color reproduction of offset lithography and other conventional processes. Multicolored images printed on the same substrate may not show perfectly uniform shades across a printed sheet. While acceptable for many applications, this poses issues for those demanding highest color fidelity.
Finishing Options
The finishing capabilities of digital presses like folding, binding, and die/slit cutting remain more basic than traditional printing lines. This constrains packaging converting, imposement of sheets, and complex structural prints. New lines integrating cutting, creasing, and even digital embossing allow better in-line finishing for some applications. But producing certain formats can necessitate off-line post-processing.
Overall, digital printing has seen phenomenal adoption growth and its applications continue expanding each year. Once limited to short-run, on-demand, and customized use cases, digital presses now match or surpass conventional processes for many standard print jobs. While not suitable for all industrial requirements, digital technology has brought accessible printing and design to countless new users worldwide. Its transforming impact on the printing industry and many other sectors will only accelerate further with ongoing innovation.
Get more insights, On Digital Printing