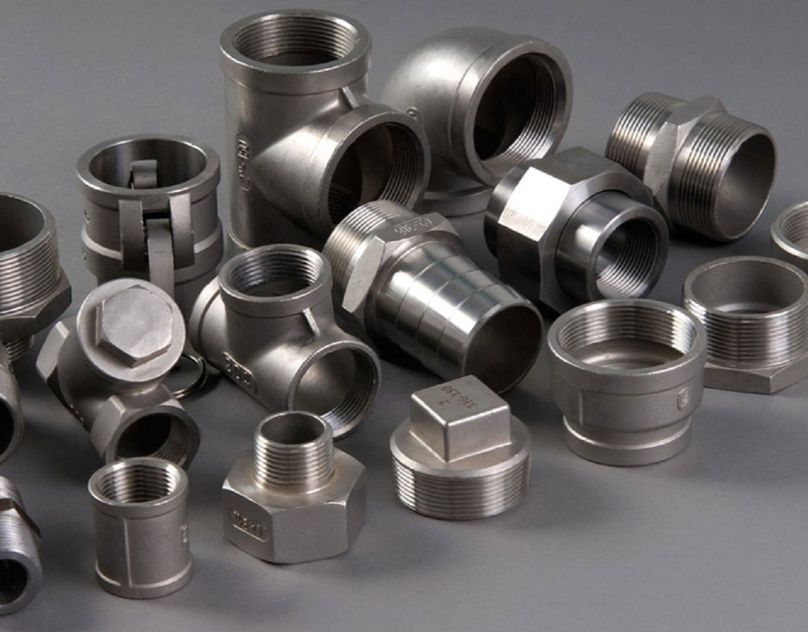
Western Steel Agency is an ANSI Forged Fittings Manufacturers in India. Forged fittings are essential in many sectors where strong and dependable pipe systems must tolerate high pressure, temperature, and corrosive conditions. The materials used to manufacture these fittings have a significant impact on their performance, durability, and appropriateness for certain applications.
Let's look at the various materials usually utilised in the production of forged fittings.
1. Carbon Steel
Carbon steel is one of the most commonly used materials for forged fittings due to its affordability, availability, and general-purpose suitability. It exhibits good strength and durability, making it suitable for applications in industries such as oil and gas, chemical processing, and power generation.
2. Stainless Steel
Stainless steel is favored for its excellent corrosion resistance properties, making it ideal for applications where the fittings are exposed to corrosive substances or environments. Its durability and hygiene make it suitable for industries such as food processing, pharmaceuticals, and marine engineering.
3. Alloy Steel
Alloy steel forged fittings are engineered to provide superior strength, toughness, and resistance to corrosion and high temperatures. They find extensive use in industries such as aerospace, automotive, and petrochemicals, where performance under extreme conditions is critical.
4. Brass
Brass forged fittings are known for their excellent machinability, corrosion resistance, and electrical conductivity. They are commonly used in plumbing, HVAC, and hydraulic systems due to their ease of installation and reliability.
5. Copper
While less common, copper forged fittings offer excellent electrical conductivity and corrosion resistance. They are primarily used in specialized applications where these properties are essential, such as in refrigeration systems and electrical installations.
6. Nickel Alloys
Nickel alloys, such as Inconel, Monel, and Hastelloy, are renowned for their resistance to high temperatures, corrosion, and chemical reactions. They are widely used in industries such as aerospace, chemical processing, and marine engineering, where extreme conditions are prevalent.
7. Titanium
Titanium forged fittings are lightweight yet strong, with exceptional corrosion resistance properties. They find applications in aerospace, marine, and medical industries where weight reduction and durability are paramount.
8. Monel
Monel forged fittings offer exceptional resistance to acids, alkalis, and corrosion, making them suitable for marine, chemical, and petrochemical industries where harsh environments are common.
9. Inconel
Inconel forged fittings excel in high-temperature applications, retaining their strength and integrity under extreme conditions. They are extensively used in aerospace, nuclear, and chemical processing industries.
10. Hastelloy
Hastelloy forged fittings are designed to withstand extreme conditions, including high temperatures, corrosive chemicals, and acidic environments. They are widely utilized in petrochemical, chemical processing, and power generation industries.
11. Duplex Stainless Steel
Duplex stainless steel forged fittings offer a unique combination of the properties of austenitic and ferritic stainless steels, including high strength, corrosion resistance, and durability. They are commonly used in offshore, marine, and oil and gas industries.
Everything You Need to Know About Forged Fittings
Western Steel Agency is an ANSI Forged Fittings Manufacturers in India. Forged fittings are essential components in various industries, providing reliable connections in piping systems. Unlike cast fittings, which are formed by pouring molten metal into molds, forged fittings are shaped by compressive forces, resulting in enhanced strength and durability.
Forged fittings come in various types, each designed to meet specific requirements in different applications. Socket weld fittings are ideal for small-diameter pipes and offer leak-proof connections, making them suitable for high-pressure environments. Threaded fittings feature screw threads for easy assembly and disassembly without welding, making them ideal for low-pressure systems and situations requiring frequent maintenance. Butt weld fittings, on the other hand, are welded directly to the pipe, providing seamless connections that minimise fluid resistance, making them indispensable in critical industries such as oil and gas.
We are the best Forged Fittings Manufacturers in India, In India, we are leading Forged Fittings Manufacturers in Mumbai and Forged Fittings Manufacturers in Rajkot.
Forged fittings must meet stringent quality standards to ensure safety and reliability. Common certifications include ASME, ASTM, and API, which certify compliance with industry-specific requirements.
Despite their durability, forged fittings may experience issues such as corrosion, leakage, and fatigue. Proper material selection, installation techniques, and maintenance practices can help mitigate these issues and prolong the lifespan of the fittings.
Forged fitting material selection is essential to guaranteeing the best possible performance, durability, and dependability of pipe systems in a variety of sectors. Every material has different qualities and benefits, therefore when choosing the best material for a certain application, it's important to take into account aspects like strength, temperature resistance, corrosion resistance, and cost.
For more details:
Website: wsaindia