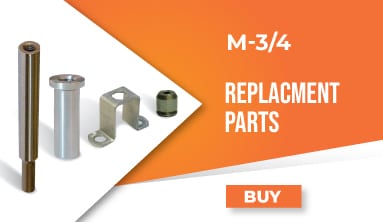
What is punching?
Punching is a widely used method in the manufacturing industry. It is used to create a large number of identical holes. Due to its ability to yield holes with optimum level of precision, it is extremely popular.
It take place with the help of punch and die tool.
Major benefits of the punching process include:
- It is capable of producing identical holes in both strip and sheet metal during medium or high production processes.
- It has the potential to create a large amount of holes that too in a meagre amount of time.
These qualities and benefits made the process of punching the best choice among other methods for creating holes of numerous varieties.
Different phases of punching a metal sheet
The process of punching is an amalgamation of three phases. Let’s discuss these phases and their importance in detail.
- Deformation
In the most simple words, when a punch is forced downwards to create a hole on the metal sheet, that action is called deformation. It is the first and foremost phase of the punching process.
The deformation usually causes significant changes in shape but not in the cross-section of the sheet.
In some cases, the magnitudes of permanent plastic and recoverable elastic deformations are comparable, therefore, elastic recovery may be significant.
Moreover, deformation processes are less energy intensive than casting processes because they are carried out at lower temperatures. The energy required in this process is far less than the thermal energy required to reach the molten stage.
- Penetration
The next phase of the punching process is penetration. In this process, the punch is forced deeper into the material which starts to penetrate the die below.
Penetration is the sum distance of the deformation and vertical burnish height. It is expressed as a percentage of the material thickness and is defined as the distance the punch must travel before the metal fractures.
The percentage of penetration differs depending on the hardness of the material. It is one of the most important phases in punching as it plays an important role in defining the quality of the final product.
- Fracture
It is the last but not the least step in the process of punching with punch and die tools. This phase is termed as fracture because in this phase the lines of fracture on both the sides of material meet and as a result, the material slug is pushed free from the blank.
It is extremely important to undertake this step efficiently as the precision of the final product highly depends on it.
Summary
Punching a hole with punch and die tool is far more versatile than drilling the hole. If we talk about size, shape, efficiency and precision, punching is a more flexible process.
The best part about punching is that it allows a vast array of shapes and sizes to be cut out, for example a square or oval shape.
Moreover, the cutting action of a drill will generate large amounts of swarf, leaving the work area covered in sharp swarf and filings whereas, you can easily avoid it by opting punching method.