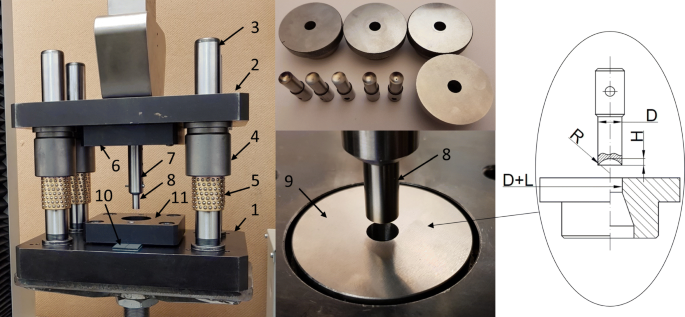
Metal punch die is widely used in numerous pockets of a manufacturing industry. They are an integral part that helps most of the sectors of industries across the globe in one-or-the-other way.
The best part of these metal punch die is that they have the capability of producing holes in all geometrical shapes and not just circular like drills. This is one of the prominent reasons behind the astronomical shift from drilling to punching in the paradigm manufacturing industry.
These square metal punch die are stronger, tougher, and often more advanced than traditional materials. To be successful, manufacturers must be equally advanced in their stamping techniques so as to ensure the longevity of these tools.
Being a manufacturer, you must know the way to operate these punching tools in a way that doesn’t deteriorate their quality and efficiency to yield precise and high quality end-products.
Let’s talk about these ways in detail.
Ways to Boost Durability Factor of Square Metal Punch Die
1. It is crucial to maintain the die
This step is crucial to avoid burrs that hinders the quality of square holes. But routine maintenance also is an imperative factor in extending punch life and reliability.
Taking the extra time for punch regrinding is well worth the effort. Making it part of your stamping routine will elevate the efficiency and life of these punching tools to an incredible level.
2. Bigger square will boost stability
Stamping tools succumb to rigid materials when they themselves lack rigidity. It is recommended to begin with die set design, engineer it with larger plates, pins, and bushings.
Using the largest, shortest (stubbiest) punch design elevates stability to the point diameter that pierces the hole, resulting in longer tool life. Together, these steps toward "bigness" will create a more rigid, durable stamping scenario.
This step will not only increase the durability factor but will help these tools to reap you highly precise square holes.
3. Reduces head breakage
Punch head breakage is one of the most common problems stampers have to face every now and then. That's the reason why it's crucial to know the nuts and bolts of alterations that make heads less vulnerable.
Drawing back the punch head to a consistent 40 to 45 Rockwell hardness C (HRC) makes it less brittle and will prevent it from the risk of breakage. Opt for making punch heads thicker and adding a larger-than-usual radius under the head.
A chamfer on the back of the punch head will reduce side loads caused by tool misalignment and will not let it affect the longevity of the tool.
4. Don’t compromise on shear angles
Manufacturers often avoid using punches with shear angles due to high die maintenance demand but this is extremely hazardous for the tool.
Sharpening is tedious but worth it. Multiple surfaces need to be maintained, and convex or concave surfaces require extra time. But all these hustles and tussles are worth the pain as shear angles significantly reduce the shock and recoil within the punch.
Wrapping it up!
Square metal punch die can pass the test of durability with flying colors but you need to be conscious while operating them. Being lenient will impact the quality of square holes.
This can cost you your manufacturing firm’s reputation as you won’t be able to serve your clients with the best of the services. And this might end up making you lose your client to your rivals.
So, don’t take the operating part frivolously, rather be conscious from the scratch.