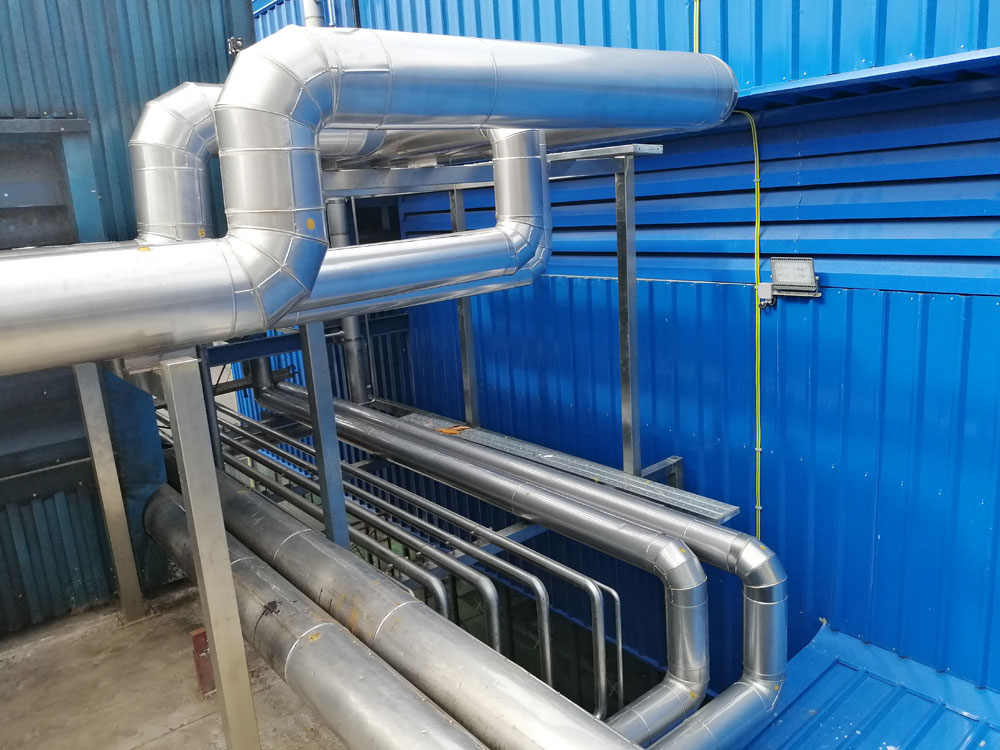
The term Process Piping System is commonly well thought-out to include the whole interconnection of pipes, including the other in-line components such as pipe fittings, flanges, Pumps, heat exchanges, valves, and tanks. The Process piping system in a way is a vital and key channel of our industrial processes and all the same, the contribution of piping systems is of a high degree in an industrialized society. The fundamental design of a process piping system is drafted and designed by the functional requirements of transporting fluid from one point to another where the design is decided by conditions such as type of fluid, pressure drop, energy loss, velocity, space, and other relevant requirements like drain temperature of liquids and so on. Nevertheless, piping systems require a significant technique, designing, fabrication, and erection works, like structural cantilevers, portals, and pedestals, which are to be specifically built for the purpose of supporting piping systems.
Industrial process piping can be carried out or installed by making use of the materials like fiberglass, glass, steel, aluminum, plastic, copper, and concrete once again dependent on the type of industry and its activities. Although the in-line components, which are generally known as fittings, such as valves, and others, that are meant to control the pressure, flow rate, and temperature of the fluid, are also included and are referred to as controlling devices in the field of piping engineering. The specification of the onsite piping layout usually within a process plant or building is referred to as drafting, technical drawing, engineering drawing, or engineering design, would be carried out manually by qualified engineers in earlier days, but nowadays it is carried out by designers using automated computer-aided drawing and design software. The material that is to be used for pipe manufacture plays a key role and must be selected according to the operating conditions of the proposed piping system.
With the main objective to ensure that the material selected is safe under the operating conditions like the pressure, temperature, corrosion, and erosion that may occur, WWG Engineering undertakes piping works with utmost care and proper technique. Steel is the most commonly used material for piping and forged steel is used for supplementary fittings while cast steel is the preferred metal for special applications where we carry out the required installations according to the client requisites. Cast iron material with high resistance to corrosion and abrasion from which we prefer it for lying of sewage lines and underground water lines, owing to its brittleness, it is not a suitable material for power plants and the company substitutes it with better materials as per the need. Our skilled engineers select Copper and copper alloys for installations in power plant pipelines where the temperature is not considered a vital and a prime factor. Technicians at WWG Engineering place emphasis on important aspects of the piping systems while connecting the pipelines. Our most preferred methods of joining to join or connect lengths of pressure piping are screwed connections, flanged connections, and welded joints, each of these methods having certain advantages and disadvantages as well, hence while constructing a joint a meticulous study and analysis of the purpose shall be taken into account by expert analysts to avoid any unsuccessful pipe lying attempts.
WWG Engineering experts contemplate uncommon fittings as comparatively expensive and require time and special materials and tools to install but yet due to their versatility, it is regarded as an important part of piping and plumbing systems too. Our experienced technicians categorize supplementary devices such as elbows, nipples, couplings, unions, tees and crosses, Y-bends, U-bends, plugs and caps, bushes, washers, and reducers, and use them accordingly. Since process piping involves an infinite intersected system including separators, flanges, hose piping, ducts and traps, strainers or sieves, gaskets or washers, and many other components which are distinctively positioned to isolate, dispense, totally stop or control and check the movement of fluids within the piping system. We study each implementation to the need and meticulously carry out the desired action accordingly.