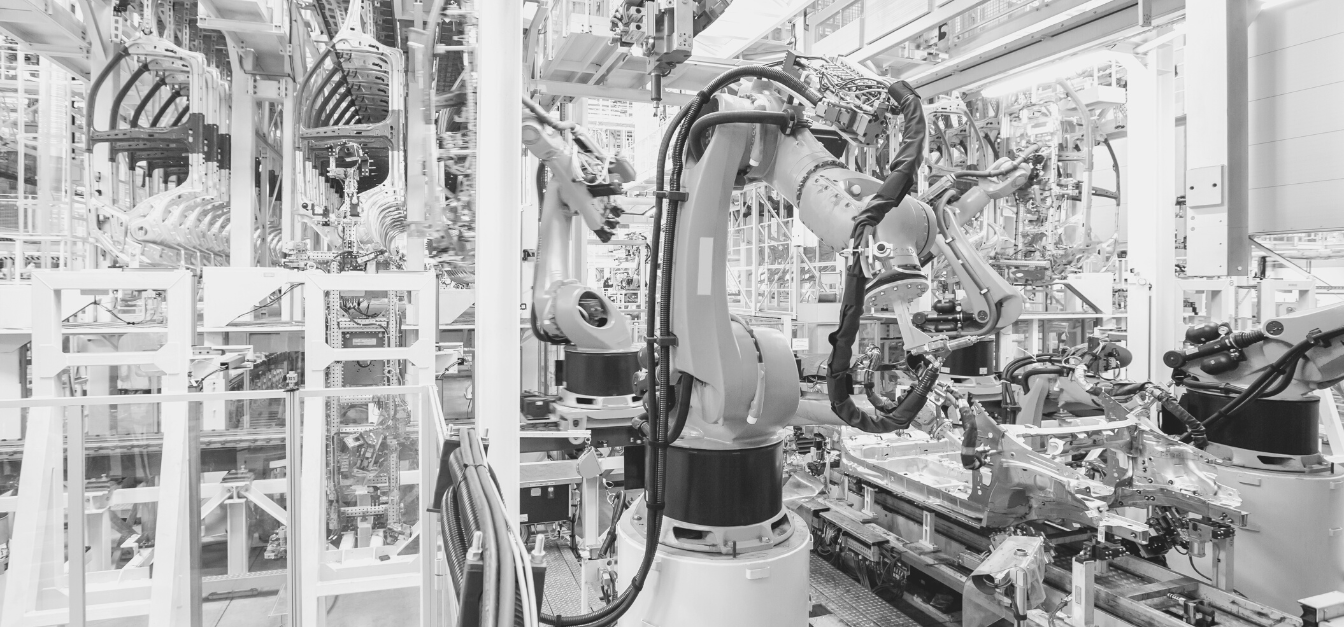
When we talk about ERP software, most of the time we are not aware of this scenario i.e., “which ERP software and what type of ERP software”.
Broadly ERP software can be classified into 3 types
- Generic ERP Software
- Manufacturing ERP Software
- Retail ERP Software
What is Generic ERP Software?
Generic ERP software is a type of software that helps businesses manage and automate their daily operations. It can be used to track inventory, customers, sales, and more. Generic ERP software is often used by small and medium-sized businesses because it is less expensive than other types of ERP software and it may not be a good fit for the manufacturer.
What is Manufacturing ERP Software?
The main goal of Manufacturing ERP software is to streamline operations and improve efficiency by giving managers a real-time view of the entire manufacturing process. ERP software for manufacturing typically includes modules for accounting, supply chain management, customer relationship management, and human resources. Manufacturing-specific ERP software also includes features such as quality control, material requirements planning, and production scheduling. However, manufacturing ERP software is largely divided into process manufacturing and discrete manufacturing.
What is a Retail ERP Software?
Retail ERP software is a system that helps businesses manage and automate their daily retail business operations, including inventory management, financials, and point of sale (POS). Retail ERP software can be used by businesses of all sizes. It covers all aspects of the business, from accounting and finance and customer relationship management and keeps track of its inventory, customers and orders.
So depending on the type of your business, a specific ERP can only fulfil the actual needs of that business. You need to identify the right ERP software for your business depending on the type of your business otherwise you may waste all your money selecting the wrong product.
Top 5 ERP Software Functionalities That Drive Manufacturing
The manufacturing module is the part of the ERP system that is responsible for managing the production process. The manufacturing module needs to be able to track all aspects of production, from raw materials to finished products.
The most common ERP modules in a manufacturing ERP are finance and accounting, manufacturing, human resources, customer relationship management and supply chain management. Other ERP modules include project management, quality management, and compliance.
While all ERP systems share these common modules, there is a lot of variation in terms of the specific functionality included in each module.
But the five most important modules functionality in a manufacturing ERP are:
- Product data management
- Quality management
- Supply chain management
- Demand planning
- Production management
1) Product Data Management:
Product data management (PDM) is a critical part of any manufacturing enterprise resource planning (ERP) system. It is the process of managing all of the data associated with a company's products, including design data, engineering data, manufacturing data, and marketing data.
An effective PDM system can help a company to streamline its operations, improve communication and collaboration between departments, and reduce costs.
2) Quality Management
Quality management is a process that ensures products and services meet customers' expectations. It is a systematic approach to planning, controlling and improving the quality of outputs from a manufacturing process.
An effective quality management system will help identify, correct and prevent problems throughout the manufacturing process. An integrated manufacturing ERP system can play a vital role in supporting quality management activities. An effective QMS helps companies to avoid costly rework, save time, and improve profitability.
3) Supply Chain Management
A supply chain is a network of suppliers, factories, warehouses, and distribution centres that work together to get products to customers. The goal of supply chain management (SCM) is to plan, execute, and control the flow of goods, information, and money across the supply chain so that the products are delivered to customers when and where they are needed.
There are four main levels of Supply Chain Management (SCM). These levels are strategic planning, tactical planning, operational planning, and finally execution and control. At each level, different decisions must be made in order to optimize the company’s SCM and in order to make these decisions ERP systems play a vital role.
4) Demand Planning
Demand planning is the process of forecasting customer demand and ensuring that the necessary inventory meets that demand. It is a key part of the production process, as it ensures that materials and finished goods are available when needed.
By accurately forecasting demand, manufacturers can avoid stockouts and excess inventory, both of which can lead to lost sales and decreased customer satisfaction. A manufacturing ERP system helps companies with demand planning by giving them visibility into past sales data, customer orders, and production capacity.
5) Production Management
Production management is the process of organizing and managing the production process to convert raw materials into finished goods. It includes the coordination of people, equipment, and resources to produce high-quality products at a lower cost and within a specified timeframe.
An effective production management system is essential for any manufacturing organization that wants to operate efficiently and stay competitive. There are three main areas of production management: people, machines, and materials and a manufacturing ERP system help production managers coordinate and manage all aspects of the manufacturing process, from people and machines to materials and inventory.
Pros & Cons of ERP systems:
There are various pros and cons of implementing an ERP system.
Pros:
- ERP software can help to automate and streamline business processes.
- It can help to improve data accuracy and visibility across an organization.
- ERP software can help to facilitate better decision-making by providing access to real-time data.
- It can help to improve customer satisfaction by providing a more efficient way to manage orders and track deliveries.
- ERP software can help to increase operational efficiency and productivity by automating tasks and reducing manual data entry.
Cons:
- The initial cost of implementing an ERP system can be high.
- Can be complex and difficult to use
- Requires significant changes to business processes and organizational structure
- There can be a steep learning curve associated with using an ERP system, and it may take some time for employees to become proficient in using the software.
- There is a risk that businesses will become too reliant on the automation provided by ERP systems. This could lead to problems if the system experiences any failure.
Conclusion:
ERP software is critical for driving manufacturing. But not all ERP software fits into the manufacturing domain. Some core features and functionality make ERP software a manufacturing ERP rest are mostly generic ERP and do not provide the in-depth functionalities required for manufacturing.
Make sure to identify which ERP software is a manufacturing ERP and which is not if you are in manufacturing and actively looking for ERP software.