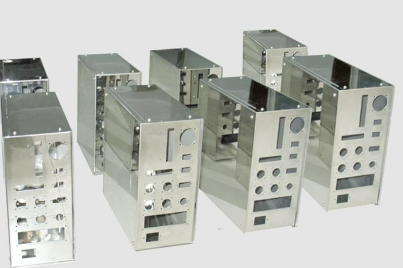
Do you wonder how a Metal Press works? A sheet metal press is simply a flatbed and a pressing ram or rod activated either hydraulically/pneumatically or mechanically. To make a metal-pressed part, insert two halves of a metal press tool into the press. You then pin the bottom of the device to the work bed and the highest of the tool to the ram or rod. Once that is done, you can feed sheet metal material into the machine, and the metal will be pressed between the two halves of the tool and will be pressed into the anticipated shape.
Multifaceted sheet metal press parts are made with advanced metal press tools. In this process, the material is fed in one direction and developments through several stages in the tool. Each step of the device adds more complication to the part by adding a bend, shearing a cut, or perforating a hole. The material is fed through occasionally, so each time the tool opens, more fabric is put in one end, and finished pressed parts come out the other.
Hydraulic and Pneumatic metal press molds use a tube and fill this liquid (including air) through a hydraulic pump. By accumulating fluid in the cylinder, the pressure builds. The force of the liquid is poured throughout the cylinder. This pressure is then exerted onto the pressing rod or ram, which creates tension down onto the tool and part to be produced. Regularly slower than mechanical presses, hydraulic presses are suitable for putting constant pressure on the entire punch length. This means they are commonly better suited for parts that need to be pressed deeply or over a long period.
Mechanical presses use an electric motor that spins a belt associated with a flywheel. This is transported through a series of gears. These gears drive the ram up and down. To start the metal press mold, the flywheel is linked to a clutch and brake system, allowing the flywheel to spin without stimulating the ram. These mechanical systems usually run faster than others, with most presses able to stamp the par 40–80 times in a minute. This rate is called Strokes Per Minute (SPM), and it’s a critical factor in advanced tool design as it commands how quickly you can make your product. The press is ideal for producing even intricate parts without much effort.