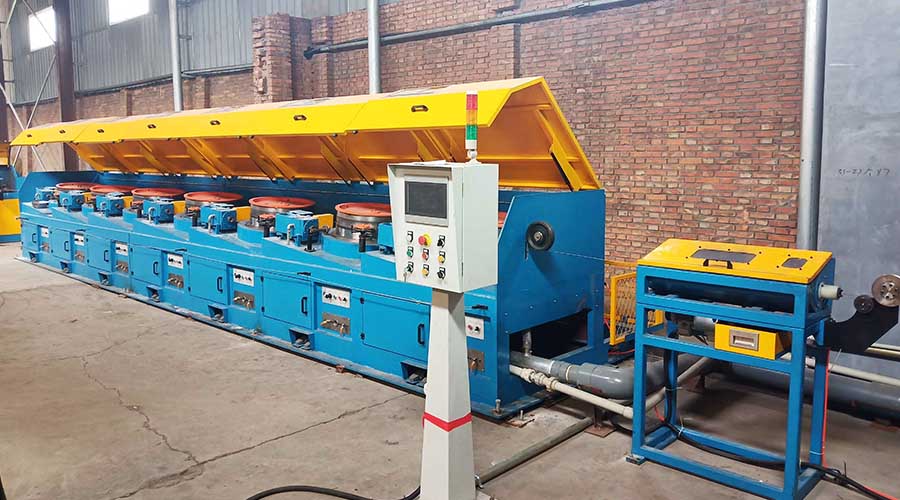
Understanding the Importance of Reduction Ratio in Wire Drawing Process: A Comprehensive Guide to Calculations
Wire drawing is a fundamental process in the manufacturing industry that involves pulling a metal wire through a series of dies to reduce its diameter. This process is widely used in various industries such as automotive, aerospace, construction, and electrical, to produce high-quality wires with specific dimensions and properties. One of the key factors that significantly impact the success of wire drawing is the reduction ratio.
What is Reduction Ratio?
The reduction ratio is a crucial parameter in the wire drawing process, which determines the degree of deformation and the final diameter of the wire. It represents the extent to which the wire diameter is reduced as it passes through each drawing die. The reduction ratio is usually expressed as a decimal or a percentage.
For example, if a wire with an initial diameter of 10mm is reduced to 5mm after passing through a drawing die, the reduction ratio can be calculated as follows:
Reduction Ratio = (Initial Diameter - Final Diameter) / Initial Diameter
Reduction Ratio = (10mm - 5mm) / 10mm = 0.5 or 50%
The Significance of Reduction Ratio
The reduction ratio plays a vital role in achieving the desired wire diameter and properties. It directly affects various characteristics of the wire, including its mechanical strength, surface finish, and dimensional accuracy.
1. Mechanical Strength:
By controlling the reduction ratio, manufacturers can precisely regulate the mechanical properties of the wire. As the wire diameter decreases, the cross-sectional area of the wire decreases as well, resulting in an increase in its tensile strength. This is because the wire material is subjected to higher compressive forces during the drawing process, which enhances its structural integrity and durability.
2. Surface Finish:
The reduction ratio also influences the surface finish of the wire. Higher reduction ratios tend to produce a smoother and more uniform wire surface due to the increased amount of metal flow and reduced surface irregularities. This is particularly crucial in applications where the wire will be further processed or used in sensitive environments where surface quality is essential, such as electrical wiring or medical devices.
3. Dimensional Accuracy:
Accurate control of the reduction ratio is critical to achieve the desired wire diameter and dimensional accuracy. The reduction ratio directly affects the amount of deformation imposed on the wire material, allowing manufacturers to precisely control the tolerances of the final product. By carefully selecting the reduction ratio, manufacturers can ensure that the wire meets the required specifications and can be easily integrated into various applications.
Determining the Ideal Reduction Ratio
Calculating the ideal reduction ratio for a wire drawing process requires careful consideration of several factors, including the material properties, desired wire diameter, and the number of drawing dies involved.
1. Material Properties:
Each material has its unique characteristics, such as ductility, strain hardening, and elastic recovery, which must be taken into account when determining the reduction ratio. Materials with high ductility, such as copper or aluminum, can tolerate higher reduction ratios without compromising their properties. In contrast, materials with low ductility, such as stainless steel or high-strength alloys, may require lower reduction ratios to avoid excessive strain or material failure.
2. Desired Wire Diameter:
The target wire diameter is a crucial factor in determining the reduction ratio. The reduction ratio needed to achieve the desired diameter depends on the initial wire diameter and the number of drawing passes. Generally, larger initial diameters require higher reduction ratios to reach the desired final diameter, while smaller initial diameters require lower reduction ratios.
3. Number of Drawing Dies:
The number of drawing dies involved in the wire drawing process also affects the reduction ratio calculation. Each drawing die reduces the wire diameter by a specific percentage, and the reduction ratios of multiple passes are multiplied together to determine the overall reduction ratio.
Calculating the Reduction Ratio
To calculate the reduction ratio for a wire drawing process, follow these steps:
Step 1: Determine the Initial and Final Wire Diameters:
Measure the initial diameter of the wire before it enters the first drawing die. Then, measure the final diameter of the wire after it passes through the last drawing die.
Step 2: Calculate the Reduction Ratios for Each Drawing Pass:
Consecutively calculate the reduction ratios for each drawing pass by dividing the difference between the initial and final diameters by the initial diameter.
Step 3: Multiply the Reduction Ratios:
Multiply all the individual reduction ratios together to obtain the overall reduction ratio for the entire wire drawing process.
Conclusion
The reduction ratio is a critical factor in the wire drawing process, significantly impacting the wire's mechanical properties, surface finish, and dimensional accuracy. By understanding the importance of reduction ratio and accurately calculating it, manufacturers can ensure the production of high-quality wires that meet the specific requirements of various industries. With precise control over the reduction ratio, manufacturers can optimize the wire drawing process and achieve the desired wire diameter with excellent mechanical strength and surface finish.
More Articles You May Interesting:
Automatic Wire Drawing Machine VS Manual Drawing Machine
Automatic Nail Making Machine Working Principle
Cemented Carbide Wire Drawing Die Manufacturing Process
Precautions for Wire Drawing Machine Operation
Elephant Trunk Type Wire Take-up Machine Features
Wire Drawing Machines: Spray Welding VS Tungsten Carbide Thermal Spraying
What is Elephant Trunk Take-up Machine?
Six Types Wire Drawing Machines
Advantages of Inverted Wire Drawing Machine
Copper Wire Drawing Machine Production Process
YF Metal Tech is a renowned wire drawing machine manufacturer.
Provide advanced wire drawing machines, auxiliary equipment, and excellent after-sales service to the metalworking industry.
After 30 years of hard work and continuous innovation, our straight line bright wire drawing machines, CO2 gas welding wire sets, stainless steel spring wire, high carbon (spring) wire drawing machines, inverted wire drawing machines and auxiliary equipment.
YF Metal Tech is the one-stop manufacturer able to design, manufacture, install, and commission your wire drawing machine plant from A to Z.
If any needs, free mail us at [email protected]
Whatsapp:+86 157 9315 9396