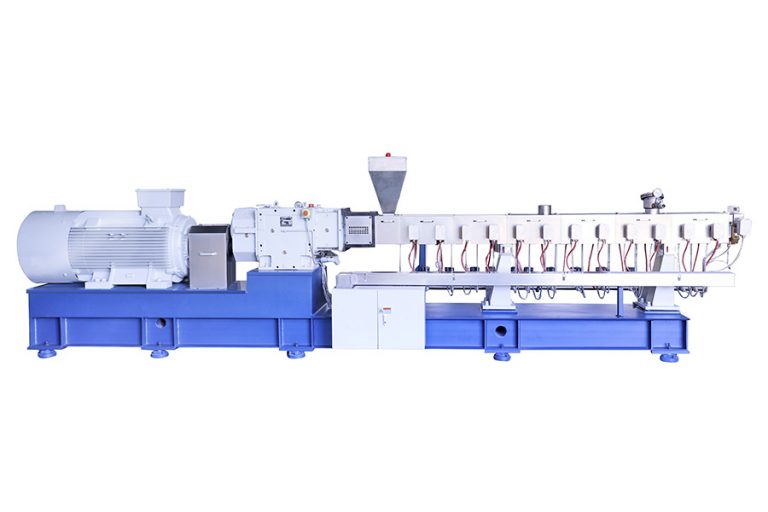
Achieving better mixing in a twin screw extruder involves optimizing various parameters and design elements of the extruder. Here are key strategies to improve mixing:
1. Screw Design and Configuration:
Screw Elements: Utilize different types of screw elements, like kneading blocks, mixing paddles, and reverse elements, to enhance distributive and dispersive mixing.
The choice of corotation versus counterrotation, as well as the design parameters of the screw, can significantly impact the mixing process. Corotating, intermeshing twin screw extruders are commonly used for mixing polymers with fillers, additives, and modifiers to impart desired performance properties.
Screw Profile: Adjust the screw profile, including the pitch, depth, and length of the flights, to influence the shear and residence time of the material.
2. Screw Speed:
Higher screw speeds can increase shear and mixing efficiency. However, it's crucial to balance speed with the thermal and mechanical sensitivity of the material to avoid degradation.
3. Barrel Temperature Profile:
Precisely control the temperature along the barrel to maintain the material at an optimal viscosity for mixing. Different zones may require different temperatures based on the material and mixing requirements.
4. Feed Rate and Fill Level:
Adjust the feed rate to ensure the extruder is neither underfilled nor overfilled. A consistent and optimal fill level aids in efficient mixing.
5. Material Properties:
Understand and adjust the formulation of the material being mixed. The rheological properties of the components can significantly affect mixing efficiency.
6. Feeding System
The selection of a feeding system for a twin screw extruder is crucial. Components may be premixed in a batch-type mixing device and volumetrically fed into the main feed. For multiple feed streams, each material is individually fed via loss-in-weight feeders into the main feed port or a downstream port. For adding fillers, reinforcements, or additional polymers, side feeders can introduce these materials at stages where primary material is already molten, improving the homogeneity of the mix.
7. Residence Time Distribution (RTD):
Optimize the residence time of the material in the extruder. Longer residence times can enhance mixing but may lead to thermal degradation for sensitive materials.
8. Back Pressure:
Adjusting back pressure using die design or valve adjustments can enhance mixing by increasing the material's residence time and shear.
9. Use of Kneading Blocks:
A twin-screw extruder works the polymer mechanically using kneading blocks to stretch, shear, and fold the polymer to generate heat. The design of the melting section affects how the material is melted, as well as melt temperature and quality.
10. Cohesive and Dispersive Mixing Zones:
Design the screw and barrel layout to create distinct cohesive (for melting and homogenizing) and dispersive (for breaking down and distributing additives) mixing zones.
11. Regular Maintenance:
Ensure screws and barrels are in good condition. Wear and tear can lead to gaps, reducing mixing efficiency and consistency.
12. Simulation and Analysis:
The metering equipment, twin-screw extruder, and downstream systems should all work in concert to control the properties of the final part and manage the process of mixing. Controls include PLCs and HMI screens with data acquisition, trending, and recipe management. Use computational tools to simulate flow and mixing in the extruder, allowing for optimization before practical trials.