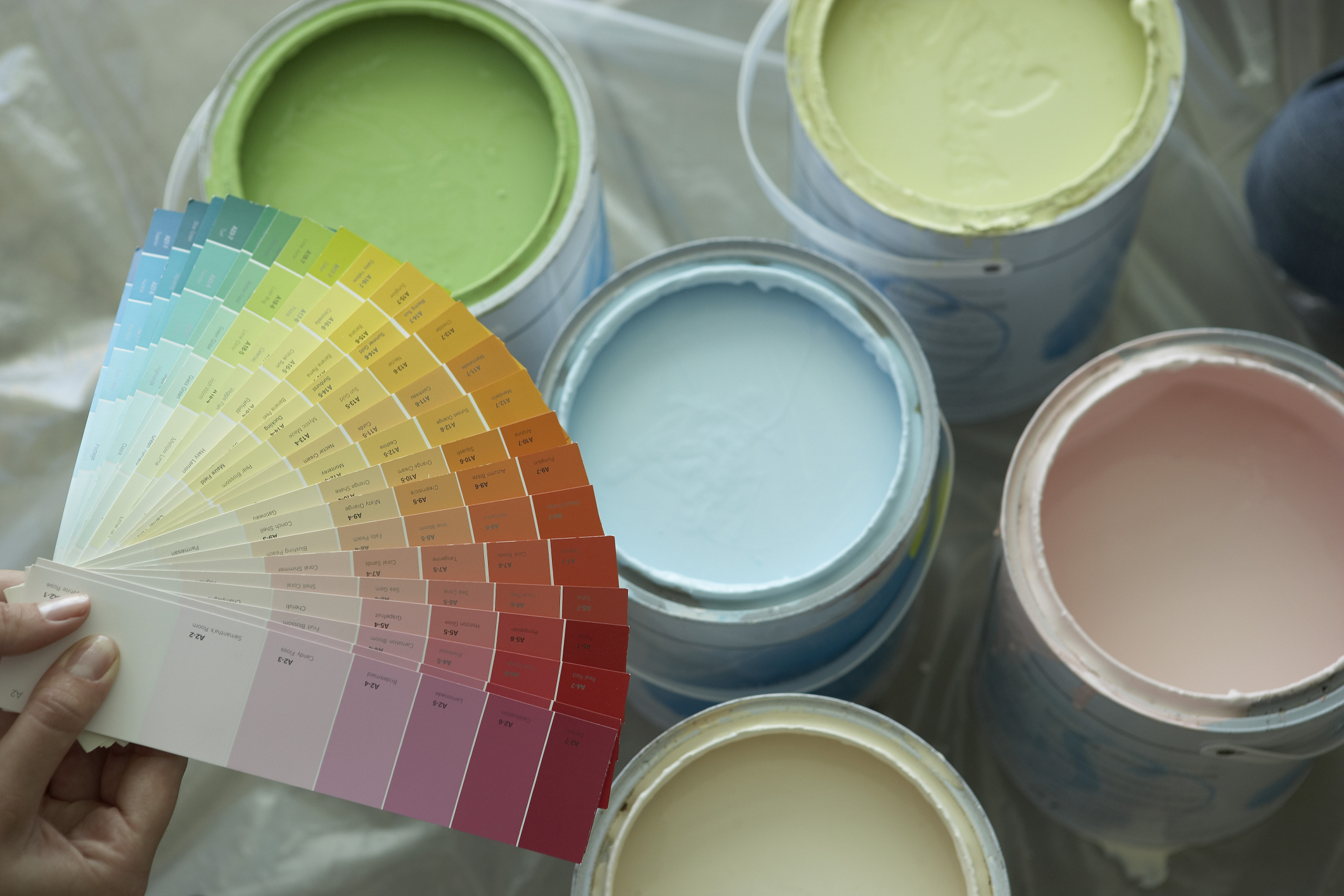
The use of tempered coatings has grown significantly in recent years across multiple industries due to the unique properties they provide. Tempered coatings undergo a careful heating and cooling process that increases their durability, hardness and resistance to breakage when stressed. In this article, we will explore the advantages of tempering coatings and how various industries are utilizing these coatings to improve safety and performance.
What are Tempered Coatings?
Tempered coatings undergo a heat treatment process called tempering where the coating material such as glass or metal is carefully heated to specific temperatures just below the annealing point and then cooled in a controlled manner. This process relieves internal stresses in the material and increases its mechanical strength. The exact tempering temperature and cooling rate depends on the material being coated but it leads to properties like higher resistance to breakage from impact or flexing forces.
Tempering essentially hardens the coating material, making it less susceptible to chips, cracks or breaks when under pressure or impact. This hardening is achieved microscopically as the internal crystal structure of the material changes during heating and controlled cooling. The result is a stronger, tougher and more durable coating compared to non-tempered versions. Tempering coatings is becoming increasingly used across industries like automotive, consumer goods and heavy machinery.
Tempered Coatings in Automotive Industry
The automotive industry has widely adopted tempered coatings to enhance safety, particularly in areas prone to impact. Automotive glass undergoes a tempering process which increases its strength by 4 times compared to regular float glass. The tempering causes the entire sheet of glass to be under compression, preventing dangerous full breakage into sharp shards if damaged. Instead, tempered glass breaks into small granular chunks, minimizing injury risk.
Beyond window glass, automakers also apply tempered coatings to other areas like side mirrors, backlights and transparent sunroofs. This helps meet modern safety standards focusing on pedestrian impact protection. Even equipment displays and control panels in vehicles nowadays utilize tempered glass coatings for their scratch resistance and shock absorbency. For heavy vehicles, tempered steel is gaining prominence for parts like dump truck payloads due to its durability under strain.
Industrial and Consumer Applications
Manufacturing and industrial equipment see extensive use of Tempered Coatings for components that undergo rigorous operational stresses. Items like drill bits, cutting tools, blades and wear parts have tempered steel or carbide coatings for their ability to retain sharpness and withstand friction or pressure. Other industrial applications include tempered glass for equipment display/control panels, warehouse skylights and commercial greenhouse glazing.
On the consumer front, nearly all tabletop glass and ceramic cookware today uses a tempering process to make them impact resistant and less prone to shattering. Safety glass for framed pictures, mirrors and home furniture also rely on tempering. Even transparent armor in bulletproof vests and ballistic shields utilizes tempered multilayer designs to absorb impact. Tempering has also found uses in renewable energy, with robust tempered coatings used for wind turbine blades and solar panel front sheets.
Quality Assurance for Tempering
While tempering enhances performance and safety of coated products, it is also crucial for manufacturers to maintain strict quality control standards during tempering. Any flaws or inconsistencies introduced can compromise the intended strength increases. Various tests are used by coaters to validate proper tempering, from simple stress crack testing to more advanced techniques:
- Ring shear testing: Measures force needed to shear a ring of coated material, indicating temper level.
- Optical emission spectroscopy: Analyzes crystal structure of tempered coating for process validation and flaw detection.
- Acoustic microscopy: Uses ultrasonic pulses to locate microscopic defects undetectable to naked eye.
- Hardness testing: Evaluates Vickers or Rockwell hardness levels compared to baseline standard.
Proper quality assurance helps tempered coatings reliably deliver on their safety and performance benefits repeatably for the product lifecycle. This ensures customer and regulatory confidence.
Tempering process creates hardened, impact-resistant coatings with widespread industrial usage spanning automotive, consumer goods, infrastructure and more. Strict quality controls during manufacturing guarantee tempered coatings provide their promised increases in durability, safety and performance longevity. As advanced materials continue joining new industrial sectors, tempered coatings will remain an essential enabling technology.
Get more insights on Tempered Coatings